Total Quality Management Benefits and Barriers
Total Quality Management (TQM) is a management approach aimed at long-term success through customer satisfaction. It focuses on continuous quality improvement in all aspects of an organization, involving all employees in the process.
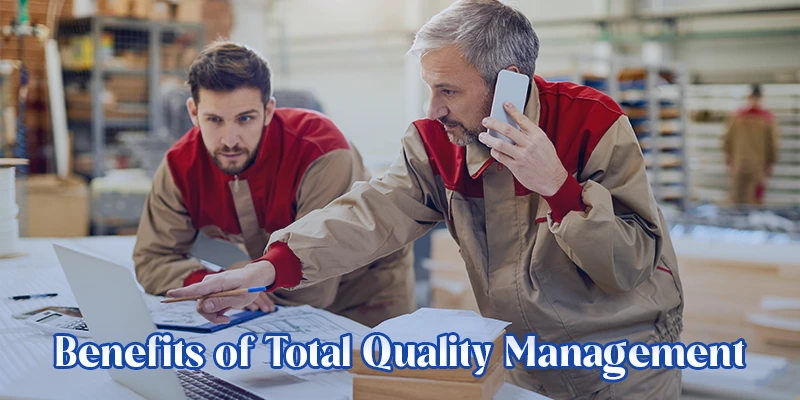
Embedding a culture of quality at all levels, enables an organization to achieve greater operational efficiency, reduce costs, and boost customer loyalty. In this blog, we will explore the key benefits that come with implementing TQM and how it can drive long-term success for businesses in any industry.
What is Total Quality Management (TQM)?
Total Quality Management (TQM) is a comprehensive management system aimed at improving the overall quality of an organization's processes, products, services, and culture. TQM focuses on continuous improvement, with an emphasis on customer satisfaction. It involves all employees at every level of the organization and integrates quality into every aspect of the business. By using strategic planning, data analysis, and effective communication, TQM creates a systematic approach to quality management that contributes to long-term organizational success.
17 Benefits of Total Quality Management
TQM brings many benefits to organizations. Here’s a look at some of them:
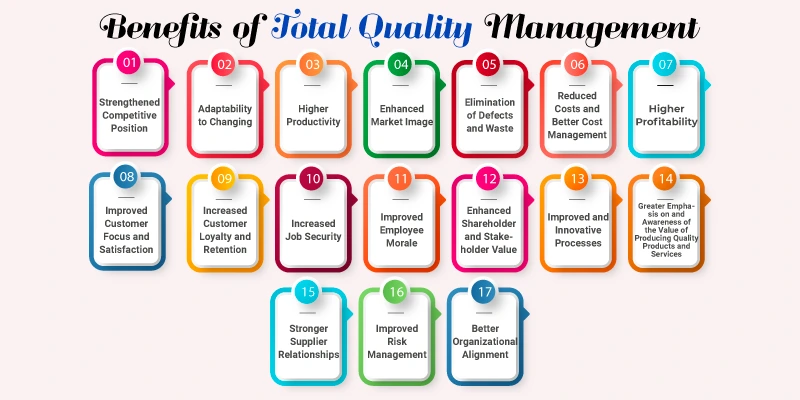
1. Strengthened Competitive Position
TQM enhances an organization's ability to compete by ensuring that it consistently delivers high-quality products and services. By focusing on continuous improvement, businesses can differentiate themselves from competitors, often resulting in increased market share and stronger positioning in their industry.
2. Adaptability to Changing or Emerging Market Conditions and to Environmental and Other Government Regulations
TQM encourages flexibility in business processes, making it easier for companies to adapt to market shifts, regulatory changes, or environmental factors. With a strong focus on continuous improvement and quality control, businesses can quickly align their operations with new regulations, consumer demands, or emerging trends, helping them stay ahead of the competition.
3. Higher Productivity
TQM improves efficiency across all business functions. By eliminating bottlenecks, streamlining processes, and reducing waste, businesses achieve higher output with the same or fewer resources. Studies have shown that companies using TQM principles see significant gains in productivity, often increasing by 15-20%. This leads to better resource utilization and a more effective workforce.
4. Enhanced Market Image
A company known for its high quality and continuous improvement processes builds a strong reputation in the market. Customers, partners, and stakeholders prefer working with businesses that are committed to delivering consistent, top-notch products or services. This enhanced reputation helps attract new customers, improve business relationships, and establish a solid brand presence.
5. Elimination of Defects and Waste
One of the core principles of TQM is to reduce defects and eliminate waste in all processes. By focusing on quality at every stage of production, from design to delivery, businesses can drastically reduce errors, rework, and waste. This results in improved product quality, reduced costs, and more efficient operations.
6. Reduced Costs and Better Cost Management
TQM helps companies identify areas where costs can be reduced, such as through process optimization, waste elimination, and improved resource management. By reducing defects and rework, companies can lower costs associated with repairs, returns, and customer complaints. Efficient operations and better cost management lead to significant savings, contributing to better financial performance.
7. Higher Profitability
Higher efficiency, cost savings, and improved customer satisfaction directly impact profitability. As defects decrease and products improve, businesses experience lower costs and higher sales due to customer loyalty and retention. Companies that implement TQM report 20-25% higher profitability over time, driven by these combined factors.
8. Improved Customer Focus and Satisfaction
TQM centers on understanding and meeting customer expectations. By prioritizing customer needs and continuously improving processes, companies can ensure higher levels of satisfaction. This focus leads to repeat business, customer referrals, and an enhanced relationship with customers, driving long-term success.
9. Increased Customer Loyalty and Retention
When customers consistently receive high-quality products and services, they are more likely to remain loyal to the brand. TQM helps businesses meet or exceed customer expectations, fostering stronger relationships. As a result, customer retention improves, and businesses see an increase in repeat sales and long-term revenue.
10. Increased Job Security
Employees in companies that implement TQM often enjoy greater job security. As the organization becomes more efficient and competitive, it is better positioned for growth and sustainability. This creates a stable work environment, where employees feel confident about their future and contributions to the company.
11. Improved Employee Morale
TQM encourages employee involvement at all levels of the organization. When employees feel that their input is valued and that they play a role in improving the business, their morale rises. Engaged employees are more motivated and productive. Studies show that higher employee satisfaction leads to 17% higher productivity and 21% higher profitability.
12. Enhanced Shareholder and Stakeholder Value
TQM contributes to long-term business success, which benefits shareholders and stakeholders. As a company improves its quality, reduces costs, and increases profitability, its financial performance strengthens. This, in turn, leads to better returns on investment for shareholders and greater value for other stakeholders, such as suppliers and customers.
13. Improved and Innovative Processes
TQM fosters a culture of continuous improvement, encouraging innovation and the refinement of processes. By constantly seeking ways to enhance product quality, businesses are more likely to introduce new ideas, technologies, or methods that improve overall efficiency and effectiveness. This innovation keeps companies competitive and able to meet evolving market needs.
Must see: Total Quality Management Tools
14. Greater Emphasis on and Awareness of the Value of Producing Quality Products and Services
Through TQM, organizations instill a deeper understanding of the importance of quality in every employee. The emphasis on quality throughout the organization helps ensure that every product or service meets or exceeds customer expectations. This shared commitment to quality leads to better outcomes and greater attention to detail at every level of the company.
15. Stronger Supplier Relationships
TQM emphasizes collaboration between organizations and their suppliers to ensure quality standards are met across the entire supply chain. By involving suppliers in quality improvement efforts and sharing best practices, companies can build stronger, more reliable relationships. This collaboration often leads to better material quality, more timely deliveries, and reduced costs for both parties.
16. Improved Risk Management
TQM helps organizations proactively identify potential risks before they become major issues. By continuously monitoring and analyzing processes, companies can spot vulnerabilities and address them promptly, reducing the likelihood of costly mistakes, delays, or product recalls. This early risk identification and mitigation lead to a more stable and secure business environment.
17. Better Organizational Alignment
TQM ensures that all departments and employees are working toward common goals, such as customer satisfaction and continuous improvement. This alignment fosters a unified company culture where everyone understands their role in delivering quality. As a result, business objectives are met more efficiently, leading to better overall performance and a more cohesive work environment.
Read More: Total Quality Management: Best Practices and Strategies
Total Quality Management (TQM) Common Challenges
Total Quality Management (TQM) offers numerous benefits, there are also some challenges or problems organizations may face during its implementation. Here are a few:
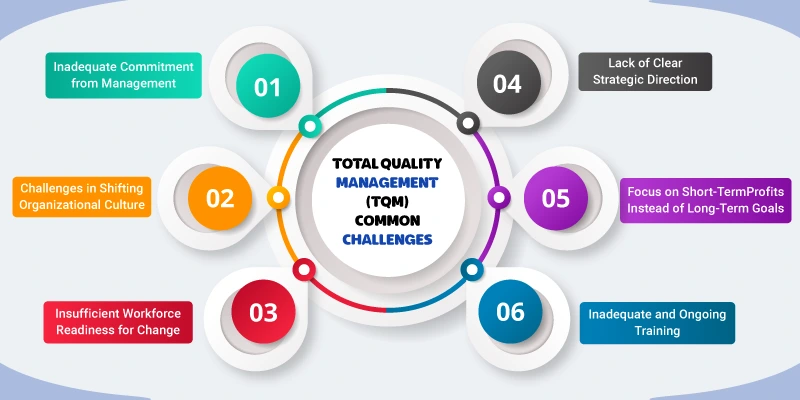
1. Inadequate Commitment from Management
Without strong, ongoing commitment from top management, TQM initiatives often lack the necessary direction and support to succeed. Leadership must not only endorse TQM but also actively participate in driving and modeling quality behaviors across the organization.
2. Challenges in Shifting Organizational Culture
TQM requires a significant shift in organizational culture, where quality becomes a core value. This cultural change can meet resistance, especially in companies with long-standing habits or practices. Overcoming this resistance requires patience, consistent messaging, and leadership.
3. Insufficient Workforce Readiness for Change
Effective TQM implementation depends on preparing employees for the changes it brings. If the workforce isn't adequately trained or informed about the new processes and expectations, it can lead to confusion, resistance, and slow adoption of TQM practices.
4. Lack of Clear Strategic Direction
Without a clear strategy and well-defined goals, TQM efforts can become disjointed and ineffective. A company must align its quality objectives with its overall business strategy to ensure that TQM becomes a driving force for success, not just a set of disconnected practices.
5. Focus on Short-Term Profits Instead of Long-Term Goals
TQM is a long-term approach to improving quality. Companies that focus too heavily on short-term gains may not have the patience to invest in TQM processes. The lack of a long-term mindset can prevent businesses from seeing the full benefits of TQM over time.
6. Inadequate and Ongoing Training
Continuous education is essential for TQM to thrive. Without regular training, employees may not fully understand TQM principles or how to apply them. Ongoing skill development ensures that the workforce remains engaged and capable of supporting quality initiatives.
AMREP Mexico: Excellence in Supplier Quality
AMREP Mexico stands at the forefront of Supplier Quality services, delivering innovative, localized solutions that enhance supplier performance and product quality. With over two decades of experience, AMREP Mexico continues to help clients achieve their production objectives with the lowest cost, highest quality, and optimal efficiency. By leveraging the power of Total Quality Management (TQM), AMREP Mexico not only drives continuous improvement but also secures long-term success for its clients and partners in an ever-evolving marketplace.