Why Quality Assurance is Crucial for Success in Every Industry
Quality Assurance is about creating a framework that helps prevent defects, enhances efficiency, and promotes continuous improvement. It’s not just about catching mistakes after they happen; it’s about embedding quality into every step of development, manufacturing, or service delivery, from start to finish. It directly impacts customer satisfaction, operational costs, brand reputation, and long-term business success. QA ensures that businesses can deliver reliable, safe, and compliant products while maintaining a high level of trust and confidence with their customers.
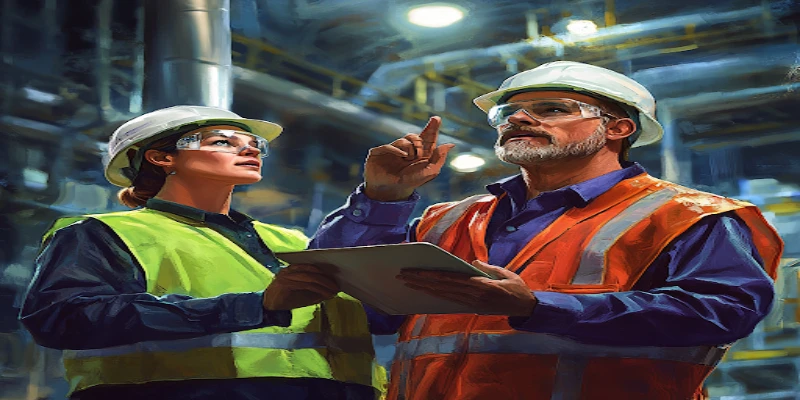
In this blog, we’ll explore why QA is essential in every industry and how it plays a critical role in achieving operational excellence.
What is Quality Assurance (QA)?
Quality Assurance (QA) is a systematic process designed to ensure that products, services, and processes meet defined standards of quality. The goal of QA is to prevent defects or problems before they occur, rather than just identifying and fixing issues after the fact. QA involves the entire process of production or service delivery, with a focus on improving and maintaining consistent quality throughout every phase.
While Quality Control (QC) focuses on identifying defects or issues in the final product, Quality Assurance is about establishing processes and standards that help prevent defects in the first place.
Read More: What Is a Quality Assurance Specialist?
Key Components of Quality Assurance
1. Standardization:
- QA involves setting clear quality standards and guidelines for processes, products, or services. These standards can be based on industry norms, regulatory requirements, or internal company policies.
- Examples include ISO certifications, Six Sigma practices, or industry-specific regulations like FDA guidelines for pharmaceuticals.
2. Process-Oriented:
- QA emphasizes creating, improving, and optimizing processes rather than focusing solely on end products. Well-defined and well-managed processes are the foundation of consistent quality.
- QA includes designing workflows, developing testing procedures, defining roles and responsibilities, and setting quality metrics for each phase of production or service delivery.
3. Prevention Over Detection:
- QA aims to prevent problems from happening at all by ensuring that processes and systems are capable of producing high-quality outputs. This contrasts with Quality Control (QC), which typically focuses on identifying defects after the fact.
- This preventive approach helps reduce the costs associated with errors, rework, and customer complaints.
4. Continuous Improvement:
- QA is closely tied to continuous improvement philosophies, such as Kaizen or Lean, which focus on making small, incremental changes to improve quality over time.
- This is an ongoing process where feedback, audits, and analysis help refine processes, products, or services.
Quality Assurance: Why It’s Essential in Every Industry
The principles of QA—such as consistency, reliability, and customer satisfaction—are universally applicable. Here’s a look at why QA is essential across all industries:
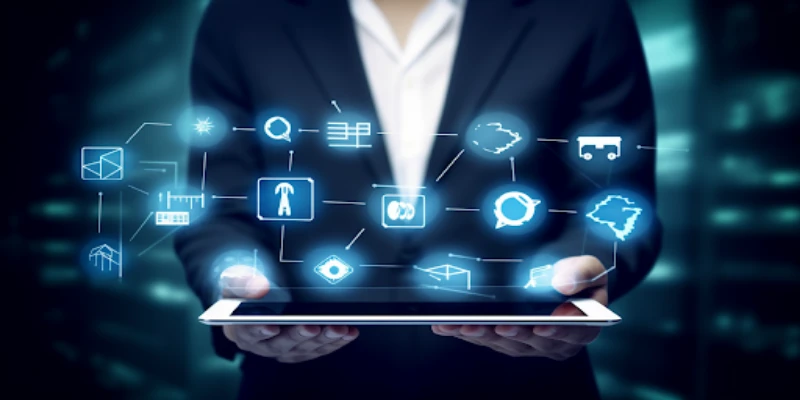
1. Customer Satisfaction and Retention
- Expectation of Quality: In today's competitive marketplace, customers expect products and services that are functional, reliable, and high-quality. Defects or failures lead to frustration, damage to reputation, and loss of business.
- Brand Loyalty: Consistent delivery of high-quality products builds brand trust, which in turn fosters customer loyalty. Customers who trust a brand are more likely to return and recommend it to others.
- Example: In the tech industry, if a software product is buggy or unreliable, users may switch to competitors, resulting in lost market share. For a food product, quality issues like contamination can have far-reaching consequences, including loss of consumer confidence.
2. Risk Management and Compliance
- Minimizing Risk: QA helps identify and mitigate risks early in the development process. This is critical in industries like healthcare, finance, and manufacturing, where errors can lead to severe consequences, including safety issues, financial loss, or legal action.
- Regulatory Compliance: Many industries are subject to strict regulations and standards that require adherence to quality guidelines. QA ensures that organizations comply with these standards, avoiding penalties and legal issues.
- Example: In pharmaceuticals, stringent QA processes ensure that drugs are safe for consumption and meet regulatory standards, which is vital for public health. In finance, quality controls ensure that transactions, audits, and financial reports are accurate and in line with legal requirements.
3. Cost Efficiency and Resource Optimization
- Preventing Costly Mistakes: Catching defects or inefficiencies early reduces the cost of fixing problems later in the process. QA ensures that time and resources are not wasted on substandard work, which can be more expensive and time-consuming to fix after production.
- Optimized Processes: QA focuses on improving operational efficiency, identifying areas where resources (time, labor, materials) are underutilized or overburdened. By streamlining processes, organizations can reduce waste and improve profitability.
- Example: In manufacturing, poor-quality components can lead to expensive recalls, rework, or production stoppages. By implementing rigorous QA standards, companies can reduce defects and avoid the costs associated with fixing them after the fact.
4. Improved Product Development and Innovation
- Continuous Improvement: QA promotes an iterative approach to product development. Through ongoing testing, feedback, and analysis, companies can make incremental improvements that lead to better products over time.
- Encouraging Innovation: With a solid QA foundation, organizations can innovate with confidence. Knowing that quality control is in place gives teams the freedom to experiment with new ideas without fear of catastrophic failure.
- Example: In software development, agile methodologies paired with continuous QA testing allow developers to quickly identify and resolve bugs, improving the final product with each iteration.
5. Operational Efficiency and Time-to-Market
- Faster Time-to-Market: A structured QA process helps companies identify problems early, ensuring that products reach the market faster and with fewer revisions. In highly competitive markets, this can be a significant advantage.
- Reduced Downtime: By maintaining consistent quality in products and services, organizations can avoid operational disruptions that occur when defects cause delays or breakdowns.
- Example: In the automotive industry, QA ensures that vehicles meet safety and performance standards before they hit the market, reducing the risk of product recalls and maintaining production schedules.
6. Competitiveness and Market Position
- Differentiation: In crowded marketplaces, QA can be a key differentiator. High-quality standards and products help companies stand out from competitors and establish themselves as leaders in their field.
- Customer Confidence: When consumers know that a company consistently delivers high-quality goods or services, they are more likely to choose it over others. Positive reviews, word-of-mouth, and repeat business are driven by consistent quality.
- Example: Luxury brands like Apple, Rolex, or Toyota’s Lexus line invest heavily in QA to maintain their reputations for superior quality. This drives consumer preference and willingness to pay a premium for their products.
7. Reputation Management
- Public Perception: A company’s reputation is one of its most valuable assets, and quality plays a central role in shaping how it is perceived. QA helps maintain a positive reputation by ensuring that every product or service meets or exceeds expectations.
- Handling Defects: In industries like food, consumer electronics, or automotive, a single quality failure (such as a faulty product or health hazard) can severely damage a company’s public image.
- Example: A food recall due to contamination, a software bug that leads to a security breach, or an automotive defect that leads to accidents all have the potential to severely harm a company’s reputation. QA helps prevent such incidents and mitigates their impact if they occur.
8. Scalability and Growth
- Consistency Across Operations: As businesses scale, maintaining product and service quality across multiple locations, production lines, or platforms becomes challenging. QA ensures that quality remains consistent regardless of the scale of operations.
- Facilitating Expansion: For organizations looking to expand into new markets, maintaining quality is essential. Adopting robust QA practices allows companies to scale operations smoothly while ensuring their products and services meet the same high standards in new regions or product lines.
- Example: Global companies like McDonald's, Coca-Cola, and Amazon rely on standardized QA processes to ensure that customers receive the same level of quality and service no matter where they are located.
9. Employee Morale and Productivity
- Clarity and Standards: A well-defined QA process helps employees understand the expectations for quality and how their work contributes to overall organizational goals. Clear guidelines lead to higher morale and greater productivity.
- Minimized Frustration: When quality issues are frequent or unresolved, employees can become frustrated with the lack of consistency, which can lead to burnout or disengagement. QA helps create a more stable and predictable working environment.
- Example: In manufacturing, workers who follow a clearly defined quality standard can take pride in their work, knowing that they’re contributing to a product that meets customer expectations. This enhances job satisfaction and reduces turnover.
10. Sustainability and Environmental Responsibility
- Waste Reduction: Quality assurance helps reduce waste by ensuring that products are designed and produced with precision, reducing errors and rework that generate unnecessary waste.
- Sustainable Practices: QA is also essential for ensuring that products comply with environmental regulations and are manufactured in an environmentally responsible way.
- Example: In industries like energy, construction, or consumer goods, implementing strong QA practices can help ensure that products are environmentally friendly, energy-efficient, and sustainably produced, reducing the company’s ecological footprint.
Read More: Quality Assurance Methods
How Does Quality Assurance Work?
Quality Assurance encompasses several activities, depending on the industry and the type of product or service. Below are some common QA practices:
1. Defining Quality Standards:
Set quality criteria and benchmarks, often based on customer requirements, regulatory standards, or industry norms.
2. Process Development and Documentation:
Design processes that help ensure product quality at every stage of production. This includes defining workflows, tools, and resources.
3. Test Planning and Execution:
Develop test plans, which may involve designing test cases, specifying testing methodologies (manual or automated), and defining success criteria. Execute the tests and document the results to identify any non-compliance with quality standards.
4. Training and Skill Development:
Provide training to employees so they are familiar with quality standards and how to adhere to them. A well-trained workforce is critical for maintaining quality at every stage of production or service delivery.
5. Audits and Reviews:
Regular audits and reviews of processes, products, and services ensure that quality standards are being met consistently. Continuous monitoring can identify areas for improvement, and the insights gathered can drive process optimization.
6. Corrective and Preventive Actions (CAPA):
If quality issues are identified, corrective actions are taken to fix the problem. Additionally, preventive actions are implemented to ensure the issue does not occur again.
7. Feedback Loops:
Feedback from stakeholders (customers, employees, vendors, etc.) is crucial for continuously improving processes and products. QA processes incorporate feedback loops to adapt and enhance standards over time.
Examples of Quality Assurance in Different Industries
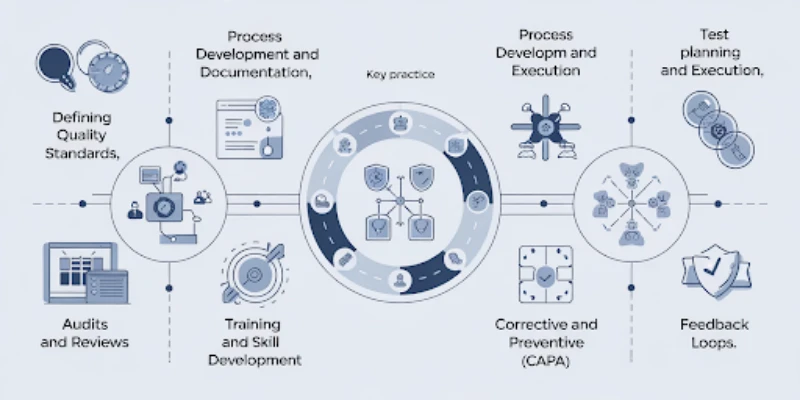
1. Software Development (Software QA):
In software development, QA involves activities such as unit testing, integration testing, performance testing, and user acceptance testing (UAT). The goal is to ensure that the software works as expected, is free from defects, and meets the requirements set by the client or end-users.
2. Manufacturing:
In manufacturing, QA ensures that products meet design specifications, safety standards, and regulatory requirements. This can involve process control, inspection, and validation to ensure that each product meets the necessary quality criteria before it leaves the production line.
Must see: Quality Assurance in Manufacturing: Ensuring Excellence and Reliability
3. Healthcare:
In healthcare, QA includes practices like ensuring medical devices meet safety standards, confirming that pharmaceuticals are manufactured under strict guidelines, and ensuring hospitals follow medical protocols to ensure patient safety.
4. Food Industry:
In the food industry, QA involves ensuring that food products meet safety and quality standards, from raw materials to the final packaged product. This can include hygiene protocols, testing for contaminants, and ensuring compliance with food safety regulations like HACCP.
5. Finance:
In the financial sector, QA involves ensuring that transactions, data handling, and reports meet regulatory standards and are free from errors. Quality assurance helps ensure that financial services operate smoothly, securely, and in compliance with laws.
QA vs. QC (Quality Control)
It’s important to differentiate Quality Assurance (QA) from Quality Control (QC), as these terms are sometimes used interchangeably but refer to different activities:
- Quality Assurance (QA) is proactive and process-focused. It aims to prevent defects by improving the processes involved in product development, production, or service delivery.
- Quality Control (QC) is reactive and product-focused. It involves inspecting and testing products or services to detect defects after they have been produced or delivered.
In essence, QA is about building quality into the process, while QC is about checking the quality of the final product.
AMREP Mexico: Excellence in Quality Assurance
At AMREP Mexico, we understand that delivering high-quality products and services is essential to building lasting relationships with our clients. That’s why we are committed to maintaining the highest standards of quality in everything we do, ensuring that each product we manufacture or service we provide meets the exacting standards our customers expect. With a relentless focus on quality, we continue to innovate and evolve, striving for excellence in every aspect of our operations.
Our Quality Control Services are designed to ensure that every product is rigorously tested and meets the highest performance standards before reaching you. Quality assurance isn’t just about meeting expectations—it’s about exceeding them. Let AMREP Mexico be your partner in delivering the best, every time.