Quality Assurance in Manufacturing: Ensuring Excellence and Reliability
Quality Assurance (QA) in manufacturing is a critical process that ensures products meet specific standards of quality, reliability, and safety. As industries evolve and customer expectations rise, effective QA practices have become essential for maintaining competitiveness and delivering value.
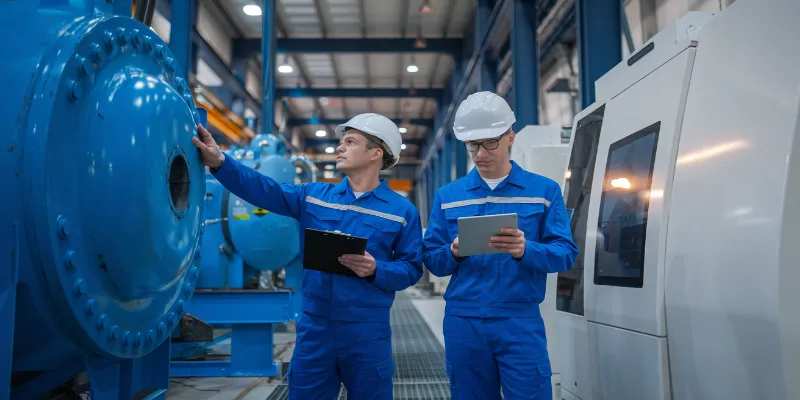
This blog will explore the vital role of Quality Assurance in manufacturing, its key components, benefits, and strategies for successful implementation. Join us as we delve into how prioritizing quality can transform your manufacturing operations and drive long-term success.
What is Quality Assurance?
Quality Assurance refers to the systematic processes implemented within manufacturing to ensure that products are designed, developed, and produced to meet specific quality standards. Unlike Quality Control (QC), which focuses on identifying defects in finished products, QA is a proactive approach that encompasses the entire manufacturing process—from initial design to final delivery.
Key Components of Quality Assurance
The key components essential to any quality assurance system, include:
- Quality Planning: Establishing quality standards and objectives for products and processes.
- Quality Control: Ongoing inspection and testing of products during the manufacturing process.
- Quality Improvement: Continuous efforts to enhance processes and product quality.
- Documentation: Maintaining records that detail quality procedures, inspections, and outcomes.
- Internal Audits: Regular assessments of quality processes and systems to ensure compliance and identify areas for improvement.
- Customer Feedback Mechanisms: Collecting and analyzing customer feedback to assess product quality and identify areas for enhancement.
- Statistical Process Control (SPC): Utilizing statistical methods to monitor and control manufacturing processes.
The Benefits of Quality Assurance
Quality assurance delivers a range of valuable benefits for manufacturers who prioritize it. Here are the key benefits of Quality Assurance (QA) in manufacturing:
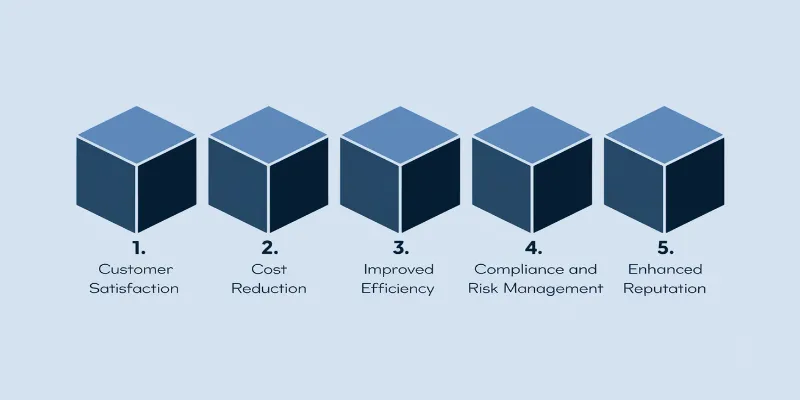
- Customer Satisfaction: A strong QA program ensures that products are reliable and meet customer expectations. Satisfied customers are more likely to become repeat buyers and brand advocates.
- Cost Reduction: Identifying defects early in the production process can significantly reduce costs associated with rework, scrap, and warranty claims. A proactive approach minimizes waste and optimizes resource utilization.
- Improved Efficiency: QA processes help streamline operations by identifying inefficiencies and bottlenecks in the manufacturing workflow. This leads to a more efficient production process and better use of time and resources.
- Compliance and Risk Management: Many industries are subject to stringent regulations. Effective QA ensures compliance with industry standards and regulations, reducing the risk of legal issues and penalties.
- Enhanced Reputation: Companies known for their high-quality products gain a competitive edge. A solid reputation for quality can lead to increased market share and brand loyalty.
The Role of Quality Assurance Tools and Techniques
Quality assurance employs a variety of tools and techniques to facilitate effective monitoring and improvement. Some key methods include:
- Failure Mode and Effects Analysis (FMEA): A systematic approach for identifying potential failure modes in a process and assessing their impact.
- Root Cause Analysis (RCA): A method for identifying the underlying causes of defects or problems to prevent recurrence.
- Statistical Process Control (SPC): Using statistical methods to monitor and control manufacturing processes, ensuring they operate at their full potential.
- Control Charts: Visual tools used to track process variability over time, helping identify trends or deviations that may indicate quality issues.
Key Strategies for Implementing Quality Assurance
Here are some key strategies for implementing Quality Assurance (QA) in manufacturing:
- Establish Clear Standards: Define quality standards that align with customer expectations and regulatory requirements. These standards should be documented and communicated across all levels of the organization.
- Employee Training: Regular training sessions ensure that employees understand the importance of quality assurance and are equipped with the necessary skills and knowledge to uphold these standards.
- Continuous Improvement: Adopt methodologies like Lean, Six Sigma, or Total Quality Management (TQM) to foster a culture of continuous improvement. Regularly review processes, gather feedback, and make necessary adjustments.
- Utilize Technology: Invest in quality management software and automation tools to monitor and analyze production processes in real time. Technologies such as IoT (Internet of Things) can provide valuable insights into equipment performance and product quality.
- Conduct Regular Audits: Implement a schedule for internal and external audits to assess compliance with established quality standards. Audits help identify areas for improvement and ensure accountability.
- Encourage Team Collaboration: Foster a collaborative environment where different departments work together to achieve quality goals. Cross-functional teams can share insights and develop solutions to common challenges.
The Future of Quality Assurance in Manufacturing
As technology continues to evolve, so too will the landscape of quality assurance in manufacturing. Here are some trends to watch:
- Artificial Intelligence and Machine Learning: These technologies will increasingly play a role in predicting defects and optimizing processes. AI can analyze vast amounts of data to identify patterns that may indicate quality issues before they arise.
- Predictive Quality: Moving from reactive to predictive quality measures will allow manufacturers to anticipate problems and address them proactively, resulting in higher overall quality.
- Sustainability and Quality: As sustainability becomes a priority, integrating quality assurance with eco-friendly practices will be essential. This includes using sustainable materials and minimizing waste while maintaining quality standards.
- Digital Twins: The use of digital twins—virtual replicas of physical processes—will enable manufacturers to simulate different scenarios and assess quality impacts without disrupting actual production.
- Remote Monitoring: With the rise of remote work and IoT technologies, manufacturers can monitor quality metrics in real-time from anywhere, enhancing oversight and responsiveness.
Challenges in Quality Assurance
While implementing quality assurance can yield significant benefits, several challenges may arise:
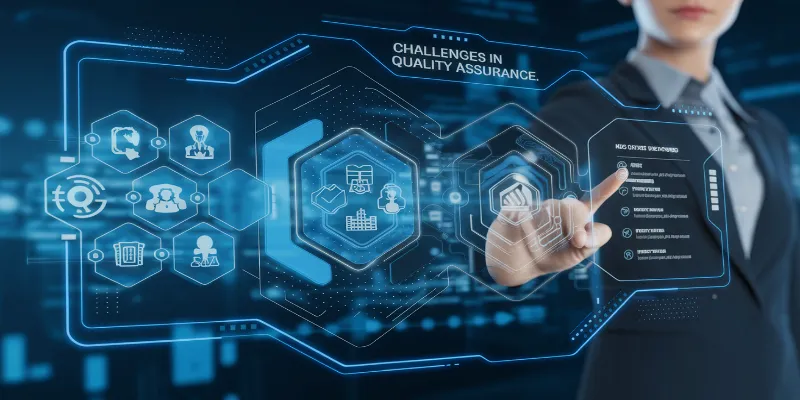
- Resistance to Change: Employees may resist new quality initiatives, making it essential to communicate the benefits and involve them in the process.
- Resource Constraints: Limited budgets and resources can hinder the implementation of comprehensive QA programs.
- Keeping Up with Technology: Rapid technological advancements require ongoing training and adaptation of QA practices to stay relevant.
- Complex Supply Chains: Globalization has led to more complex supply chains, making it challenging to ensure quality across all suppliers and partners.
Enhance your Quality Assurance system at AMREP Mexico
At AMREP Mexico, we recognize that a robust Quality Assurance system is vital for maintaining our commitment to excellence and customer satisfaction. By prioritizing quality at every stage of production, we not only ensure compliance with industry standards but also foster a culture of continuous improvement.
Join us in our journey towards excellence as we continue to enhance our Quality Assurance system, ensuring that every product we deliver meets the exceptional quality our customers expect. Your partnership and feedback are invaluable as we strive to set new benchmarks in quality and service.