Quality Assurance (QA) Basics: Components, Methods, Pros & Cons
Quality Assurance (QA) refers to the systematic process of ensuring that products and services meet specific requirements and standards before they reach the end user. At its core, QA involves a proactive approach to quality management, focusing on continuous improvement and the implementation of best practices. This includes everything from defining quality standards and conducting audits to testing products and gathering feedback.
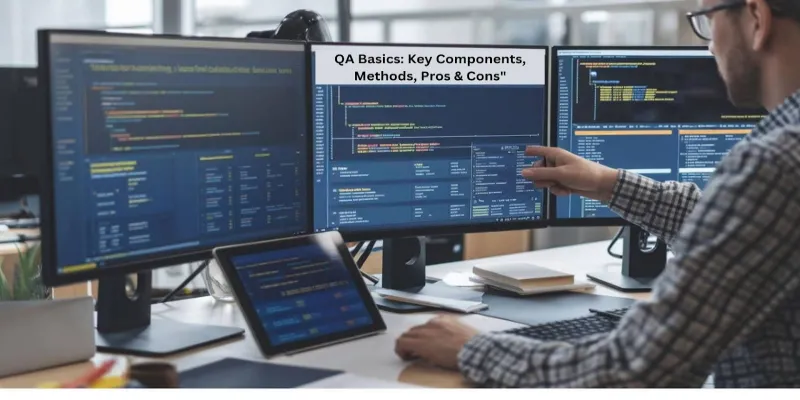
But what exactly does QA stand for, and why is it so crucial? This blog aims to clarify the fundamentals of Quality Assurance, its significance in various industries, and how it contributes to organizational success.
What Does QA Stand For?
QA stands for Quality Assurance, a systematic process that ensures products and services meet defined quality standards. It encompasses a range of activities aimed at preventing defects, improving processes, and ensuring that customer expectations are met or exceeded. QA is not merely about checking for errors; it involves creating a culture of quality throughout the entire organization.
The Importance of Quality Assurance
Quality assurance (QA) is a critical aspect of any organization, particularly in industries where product reliability and customer satisfaction are paramount. Here are some key points highlighting its importance:
1. Enhancing Customer Satisfaction
The primary goal of QA is to ensure that customers receive products and services that meet their needs. High-quality offerings lead to greater customer satisfaction, which is essential for building trust and loyalty. Satisfied customers are more likely to return and recommend the brand to others.
2. Reducing Costs
Investing in QA can lead to significant cost savings. By identifying defects early in the production process, organizations can avoid costly reworks, returns, and warranty claims. Additionally, a focus on quality helps prevent potential issues that could lead to expensive legal actions or recalls.
3. Improving Operational Efficiency
QA encourages organizations to examine their processes critically. This leads to the identification of inefficiencies and areas for improvement. Streamlined processes result in better resource allocation, faster production times, and overall improved operational efficiency.
4. Facilitating Compliance
Many industries are subject to strict regulatory standards. QA ensures that organizations adhere to these regulations, reducing the risk of legal penalties and enhancing credibility in the marketplace. Compliance with industry standards also boosts customer confidence in the brand.
5. Fostering Continuous Improvement
A robust QA framework promotes a culture of continuous improvement. It encourages teams to regularly evaluate their processes, gather feedback, and implement changes that enhance quality. This mindset not only benefits current offerings but also drives innovation and adaptability.
Key Components of Quality Assurance
Quality assurance (QA) involves several key components that work together to ensure products and services meet specified standards. Here are the essential components:
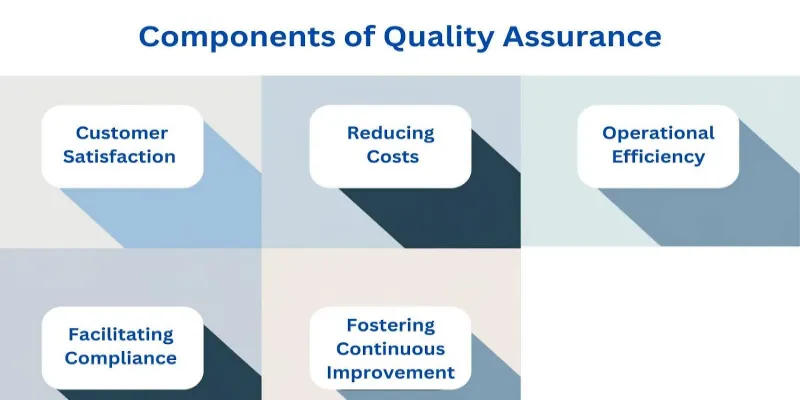
1. Quality Planning
Quality planning involves defining quality standards and determining the processes required to achieve them. This sets the groundwork for what is expected from products and services.
2. Quality Control (QC)
While QA focuses on preventing defects, Quality Control involves monitoring and evaluating specific outputs to ensure they meet the defined standards. QC is often a reactive process that identifies defects after they occur.
3. Quality Improvement
This involves analyzing data and feedback to identify areas where processes can be enhanced. Quality improvement initiatives help organizations stay competitive by continually raising their standards.
4. Documentation and Training
Proper documentation of processes and quality standards is essential for maintaining consistency. Training employees on these standards ensures that everyone understands their role in maintaining quality.
QA Methods
Quality Assurance employs various methods and techniques to ensure quality throughout the process. Here are some commonly used QA methods:
1. Statistical Process Control (SPC)
SPC uses statistical methods to monitor and control processes. By analyzing data from production, organizations can identify variations and take corrective actions before defects occur.
2. Failure Mode and Effects Analysis (FMEA)
FMEA is a proactive tool used to identify potential failure modes in a product or process and assess their impact. This method helps prioritize risks and implement measures to mitigate them.
3. Root Cause Analysis (RCA)
RCA is used to identify the underlying causes of defects or issues. By addressing the root cause rather than just the symptoms, organizations can implement effective solutions to prevent recurrence.
4. Quality Audits
Regular quality audits evaluate processes and systems against established standards. These audits help ensure compliance and identify areas for improvement.
5. Benchmarking
Benchmarking involves comparing processes and performance metrics with industry standards or best practices. This helps organizations identify gaps and areas for enhancement.
6. Continuous Improvement (Kaizen)
The Kaizen philosophy promotes continuous improvement through small, incremental changes. This method encourages all employees to contribute to enhancing quality and efficiency.
7. Test-Driven Development (TDD)
In software development, TDD is a practice where tests are written before the actual code. This ensures that all functionalities are tested and meet the specified requirements.
Quality Assurance in Different Industries
Quality assurance (QA) is essential across various industries, though its specific practices and standards may differ based on industry requirements and regulations. Here’s an overview of QA in several key sectors:
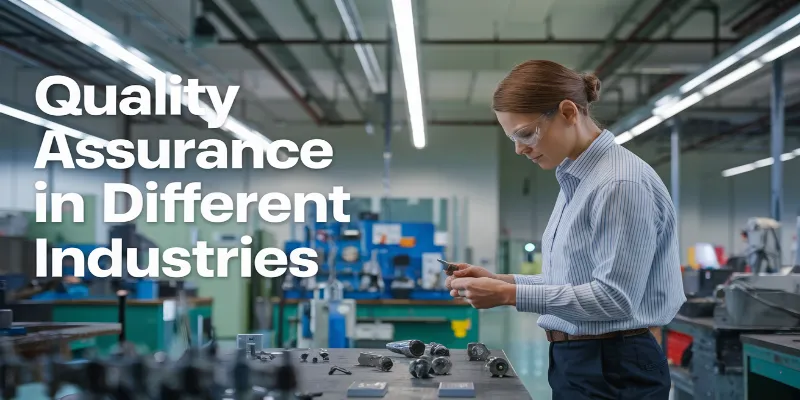
1. Manufacturing
In manufacturing, QA is crucial for ensuring that products are made to specifications. This involves rigorous testing and inspection processes to identify defects before products reach the market.
2. Software Development
In the software industry, QA ensures that applications are functional, reliable, and user-friendly. Techniques such as automated testing, code reviews, and user acceptance testing are commonly used to maintain quality.
3. Healthcare
In healthcare, QA is essential for ensuring patient safety and compliance with regulations. It involves monitoring processes, conducting audits, and implementing best practices to enhance care quality.
4. Food Industry
Quality Assurance in the food industry focuses on ensuring that products are safe for consumption and meet regulatory standards. This includes rigorous testing for contaminants and adherence to hygiene practices.
Pros and Cons of Quality Assurance
Pros
- Improved Quality: Ensures that products and services consistently meet quality standards.
- Increased Customer Satisfaction: High-quality offerings lead to greater customer loyalty and repeat business.
- Cost Savings: Identifying defects early reduces costs related to rework, returns, and warranty claims.
- Enhanced Reputation: A strong commitment to quality enhances brand credibility and trust in the marketplace.
- Risk Mitigation: Proactively addressing potential issues reduces the likelihood of compliance violations and legal actions.
Cons
- Initial Investment: Implementing a QA system requires significant time and financial resources upfront.
- Complexity: Developing and maintaining a comprehensive QA program can be complex and challenging.
- Resistance to Change: Employees may resist changes in processes and practices, impacting the implementation of QA initiatives.
- Time-Consuming: Regular audits and assessments can be time-intensive, potentially slowing down production.
- Overemphasis on Process: A strong focus on QA processes may lead to bureaucracy, stifling innovation and agility.
Quality Assurance is more than just a set of processes; it is a philosophy that underpins successful organizations. By prioritizing QA, businesses can enhance customer satisfaction, reduce costs, improve operational efficiency, and foster a culture of continuous improvement. As markets become increasingly competitive, the importance of Quality Assurance will only continue to grow, making it an essential aspect of any successful business strategy. Understanding the basics of QA, its methods, and its pros and cons is the first step toward leveraging its benefits for organizational success.
At AMREP Mexico, our commitment to Quality Assurance drives us to exceed industry standards and enhance customer satisfaction. Together, we strive to make quality a hallmark of everything we do, ensuring trust and reliability in our products and services.