Quality Control in Aerospace Industry
The aerospace industry is one of the most regulated sectors in the world. It operates in a high-stakes environment. Aircraft and spacecraft carry people and goods over long distances. Ensuring these systems are safe and reliable is non-negotiable.
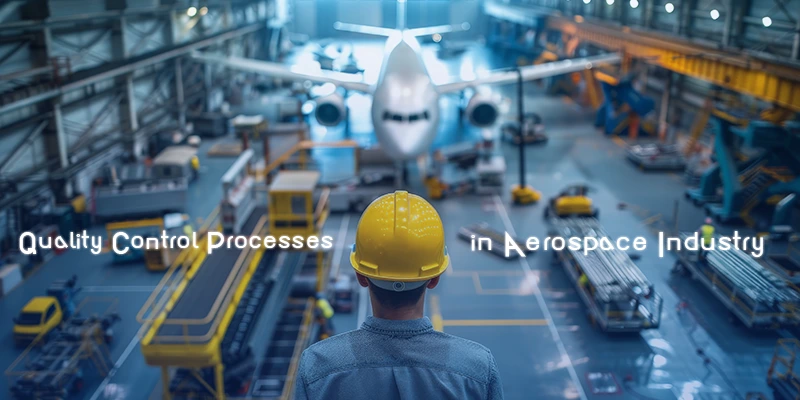
Quality control processes help prevent defects, ensure consistent performance, and maintain safety standards. It is not just about meeting regulations—it's about ensuring every product performs as expected, even in the most challenging conditions.
Regulatory Requirements and Standards in Aerospace
The aerospace industry is highly regulated to ensure the safety, reliability, and compliance of aircraft and spacecraft. Strict standards govern every stage of manufacturing, from design to maintenance.
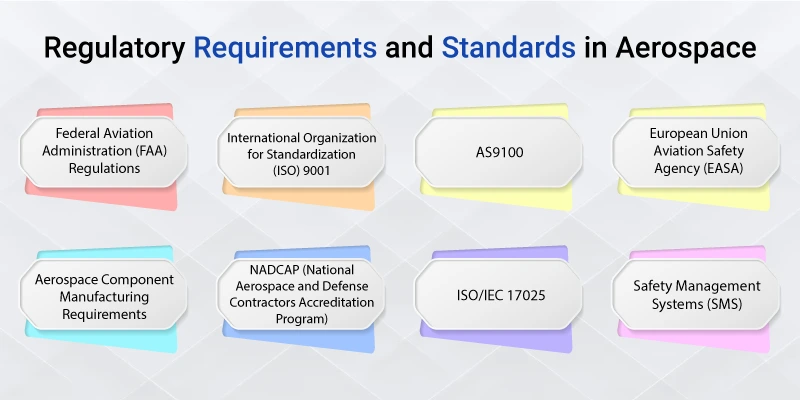
1. Federal Aviation Administration (FAA) Regulations
In the United States, the FAA sets the standards for safety and operational efficiency in civil aviation. The FAA’s regulations, such as the Code of Federal Regulations (CFR) Title 14 (known as FAR), outline rules for the certification of aircraft, components, and operations. It ensures that manufacturers, maintenance providers, and other entities meet safety standards through rigorous quality control processes.
2. International Organization for Standardization (ISO) 9001
ISO 9001 is a globally recognized standard that sets criteria for a quality management system (QMS). Aerospace companies often implement this standard to ensure they consistently provide products and services that meet customer and regulatory requirements. It focuses on continuous improvement, customer satisfaction, and risk management.
3. AS9100
AS9100 is the widely recognized international standard for quality management systems specifically in the aerospace sector. It builds on ISO 9001 and includes additional requirements specific to aerospace, such as product safety, traceability, and risk management. The AS9100 standard is crucial for manufacturers of aerospace products to ensure compliance with both customer and regulatory expectations.
4. European Union Aviation Safety Agency (EASA)
EASA is the regulatory body in Europe that establishes safety and environmental standards for aviation. Similar to the FAA, EASA sets stringent quality control requirements for the design, production, and maintenance of aerospace products. Companies in Europe must adhere to these standards for market access and safety certification.
5. Aerospace Component Manufacturing Requirements
Components used in aerospace applications are subject to stringent standards such as MIL-STD (Military Standards) and RTCA DO-160 (Environmental Conditions and Test Procedures for Airborne Equipment). These documents set criteria for testing and validating materials, components, and equipment in various aerospace environments, ensuring reliability under extreme conditions.
6. NADCAP (National Aerospace and Defense Contractors Accreditation Program)
NADCAP is an industry-managed program that certifies aerospace suppliers in areas like materials, heat treating, welding, and non-destructive testing (NDT). It ensures suppliers meet specific quality standards and helps reduce the risk of defects in critical components.
7. ISO/IEC 17025
This standard is used for the competence of testing and calibration laboratories. It ensures that laboratories involved in aerospace product testing meet specific technical requirements and can produce valid and reliable results in their quality control processes.
8. Safety Management Systems (SMS)
SMS is a systematic approach to managing safety risks in aerospace operations. It involves continuous monitoring and assessment of potential hazards, ensuring that quality control processes identify and mitigate safety risks before they become problems.
Key Quality Control Processes for the Aerospace Industry
The complexity of aerospace systems requires strict attention to detail and rigorous testing throughout the production process. Below are some of the key quality control processes that aerospace manufacturers follow to meet regulatory requirements and industry standards.
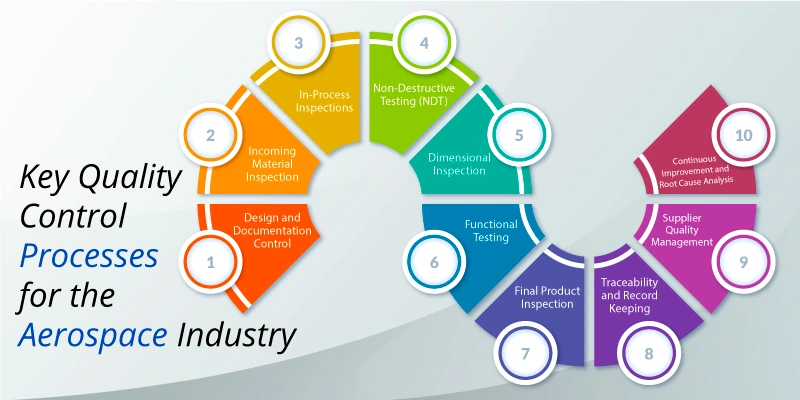
1. Design and Documentation Control
The quality control process begins in the design phase. Engineers must ensure that the design meets all safety and performance standards. Every aspect of the design is documented thoroughly to provide traceability throughout production. This includes materials specifications, engineering drawings, and testing protocols. Documentation control ensures that no changes to the design go unnoticed and that the final product conforms to the original specifications.
2. Incoming Material Inspection
Before production begins, all materials used in manufacturing are inspected to verify that they meet the required quality standards. This includes checks for material composition, strength, and durability. Commonly used materials such as metals, composites, and polymers are tested to ensure they meet the necessary criteria for performance in extreme conditions. Any materials that do not meet specifications are rejected to avoid defects in the final product.
3. In-Process Inspections
Quality control doesn’t end with incoming materials. Throughout the manufacturing process, regular inspections are performed to check for any deviations from specifications. These in-process inspections can include visual checks, measurements, and non-destructive testing (NDT). Techniques like ultrasonic testing, X-rays, and eddy current testing are used to ensure parts are free of internal flaws that might not be visible on the surface. These checks ensure that any defects are detected early, minimizing waste and rework.
4. Non-Destructive Testing (NDT)
NDT plays a crucial role in quality control for aerospace components. It involves inspecting parts without damaging them, allowing for the detection of internal defects such as cracks, porosity, or material inconsistencies. Common NDT methods used in the aerospace industry include:
- Ultrasonic Testing (UT): Uses high-frequency sound waves to detect internal flaws.
- X-ray Inspection: Provides detailed images of the internal structure of parts.
- Eddy Current Testing: Detects surface and sub-surface cracks and defects.
- Magnetic Particle Testing: Used for detecting surface defects in ferromagnetic materials.
5. Dimensional Inspection
Accuracy is crucial in aerospace manufacturing. Components are inspected using precise measurement tools to ensure they match the design specifications. This includes checking tolerances, surface finish, and alignment. Dimensional inspections are performed using tools like calipers, micrometers, and coordinate measuring machines (CMMs) to ensure that every part fits and functions correctly within the larger system.
6. Functional Testing
Once the components are assembled, functional testing is performed to verify that the part or system operates as intended. For example, engines may undergo testing to check for fuel efficiency and performance, while avionics systems are tested for accuracy in communication and navigation. These tests simulate real-world conditions to ensure reliability and performance. All systems must meet the standards set by regulatory bodies like the FAA or EASA before they can be approved for use.
7. Final Product Inspection
Before a product is shipped or delivered, it undergoes a comprehensive final inspection. This inspection ensures that all parts and systems meet the required safety and performance standards. The final product is also tested for compliance with regulatory certifications, such as FAA Part 21 (certification of aircraft). This process often involves a detailed review of documentation, compliance checks, and thorough functional testing.
8. Traceability and Record Keeping
Traceability is a fundamental part of quality control in aerospace. Every component must be tracked through every stage of production. This includes documenting raw materials, manufacturing processes, inspections, and test results. Traceability ensures that if a defect is discovered in the future, it can be traced back to its source, whether that’s a specific batch of material or a particular manufacturing process. Detailed records also serve as proof of compliance with industry standards and regulations.
9. Supplier Quality Management
Aerospace manufacturers rely heavily on a network of suppliers for raw materials, components, and sub-assemblies. Quality control extends to these suppliers through rigorous audits, inspections, and certification processes. Suppliers must meet strict quality standards, often complying with certifications like AS9100 and NADCAP. Continuous monitoring and audits ensure that suppliers maintain these standards and that quality is consistent throughout the supply chain.
10. Continuous Improvement and Root Cause Analysis
Quality control doesn’t end with the final product. Aerospace companies continually strive to improve their processes. If a defect or failure occurs, a root cause analysis is performed to determine why it happened. The goal is not only to fix the immediate problem but also to implement corrective actions to prevent similar issues in the future. Continuous improvement is an ongoing process that includes data analysis, process optimization, and feedback loops to enhance product quality.
Supplier Audits in the Aerospace Industry
Supplier audits are a critical component of quality management in the aerospace industry. These audits ensure that suppliers meet the required standards and regulations. Below are the key types of supplier audits:
- Supplier Verification: This audit checks the supplier's ability to meet contractual requirements. It confirms their capacity to provide quality products on time.
- Supplier Quality Audits: These audits assess the supplier’s quality management processes. They ensure the supplier consistently produces components that meet aerospace industry standards.
- ISO 9001 Quality Management System Audits: This audit verifies that the supplier’s quality management system aligns with the ISO 9001 standard. It focuses on continuous improvement and customer satisfaction.
- AS9100 Quality Management System Audits: AS9100 audits are specific to aerospace. These audits evaluate whether the supplier follows the quality management practices required for aerospace and defense manufacturing.
- ISO 14001 Environmental Management System Audits: This audit ensures that the supplier adheres to environmental regulations. It focuses on minimizing environmental impact and managing sustainability efforts.
- ISO 45001 Health and Safety Management Audits: These audits assess the supplier’s workplace safety practices. They ensure that the supplier follows standards to protect employees from health and safety risks.
- Social Compliance Audits: Social audits focus on the supplier’s adherence to ethical practices. This includes fair labor practices, human rights, and working conditions.
- Combined Audits: Some audits combine multiple areas, such as quality, environmental, and social audits, into one comprehensive assessment. This helps streamline the audit process and ensures all requirements are met.
These audits ensure aerospace suppliers maintain the highest standards, reduce risks, and foster long-term partnerships.
AMREP Mexico: Your Partner in Aerospace Quality Control
At AMREP Mexico, we are committed to providing world-class supplier quality management solutions for the aerospace sector. Our expertise in supplier audits, regulatory compliance, and continuous improvement helps ensure that your aerospace components meet the highest industry standards. Partner with AMREP Mexico for dependable, top-tier solutions in aerospace quality control.