Quality Control in Manufacturing: A Comprehensive Guide
Ensuring consistent quality in manufacturing is essential for building trust, exceeding customer expectations, and achieving operational excellence. Quality control (QC) is not just a technical process—it’s a cornerstone of successful manufacturing that impacts every production stage, from sourcing raw materials to delivering finished products. Manufacturers can minimize defects, lower costs, and maintain a competitive edge in their industries by adopting rigorous QC measures. Let’s discuss the critical aspects of quality control and its transformative potential in manufacturing.
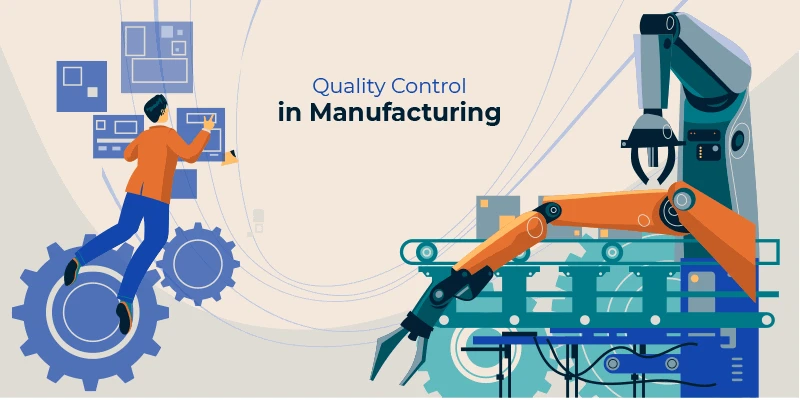
The Role of Quality Control in Manufacturing
Quality control serves as a safeguard to ensure products meet established standards and specifications. It goes beyond merely detecting flaws; it’s a proactive approach that enhances efficiency, reduces waste, and ensures customer satisfaction. For instance, well-executed QC measures allow manufacturers to identify production bottlenecks and optimize resources effectively.
A scholarly definition of Quality says that:
“We engage in quality control in order to manufacture products with the quality which can satisfy the requirements of Consumers. The mere fact of- meeting national standards or specifications is not the answer. It Is simply insufficient.”
Key Features of Quality Control
- Defect Prevention: QC protocols catch issues before they escalate into major problems, saving time and resources.
- Streamlined Processes: A robust QC system ensures consistent quality, which helps in reducing production delays and rework.
- Enhanced Reputation: Companies with strong QC frameworks earn customer loyalty and stand out in competitive markets.
Examples of QC Tools and Techniques
Tools such as digital calipers, automated inspection systems, and statistical process control (SPC) methods allow manufacturers to monitor and maintain product quality. By using these tools, organizations can:
- Track dimensional accuracy with high precision.
- Detect inconsistencies early and implement corrective actions.
- Ensure compliance with stringent industry regulations.
Table: Benefits of Implementing Quality Control
Benefit | Impact on Manufacturing |
---|---|
Reduced Defects | Lower rework costs and improved customer trust |
Enhanced Efficiency | Streamlined processes and reduced production time |
Cost Optimization | Better resource allocation and minimized waste |
Improved Reputation | Higher customer satisfaction and repeat business |
Key Components of Quality Control
QC involves an integrated approach that starts from the very beginning of the production process, ensuring that every stage contributes to achieving the desired quality standards.
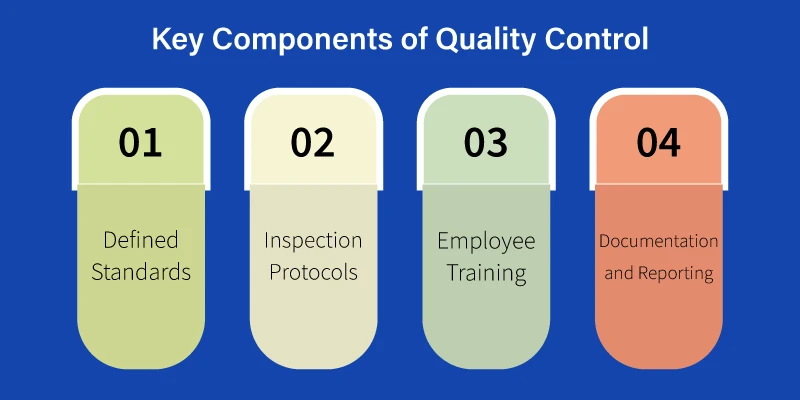
Defined Standards
Establishing clear and measurable quality benchmarks is the foundation of any effective quality control system. Standards should:
- Be industry-specific, addressing the unique needs of the sector (e.g., dimensional tolerances in manufacturing or chemical purity in pharmaceuticals).
- Include raw material specifications, production tolerances, and finished product criteria.
- Be documented in a format accessible to all stakeholders to ensure transparency and compliance.
- Evolve over time based on regulatory changes, technological advancements, and customer feedback.
Example: A manufacturer of electronic components might define standards for voltage tolerance, ensuring products meet performance expectations under varying conditions.
Inspection Protocols
Consistent and thorough inspection protocols are critical for identifying and addressing defects before products reach the customer. Effective inspection protocols should:
- Define key inspection points within the production process, such as incoming materials, in-process stages, and final products.
- Use a combination of manual and automated inspections to ensure precision.
- Include sampling methods (e.g., random sampling or full batch inspections) tailored to production volume and complexity.
- Ensure inspections are aligned with established benchmarks to identify nonconformities quickly.
Example: In an automotive assembly line, inspections might include verifying the torque of bolts, testing electrical systems, and ensuring the alignment of body panels.
Employee Training
Quality control is only as strong as the people executing it. Well-trained employees are essential to maintaining and improving quality standards. Training programs should:
- Cover technical skills, such as using inspection tools, understanding blueprints, and applying statistical quality control techniques.
- Include soft skills, like problem-solving and effective communication, to foster collaboration across departments.
- Provide ongoing education to keep employees updated on new technologies, standards, and methodologies.
- Be customized to different roles, ensuring each team member understands their responsibilities in the quality control process.
Example: Training operators on Six Sigma principles can help reduce process variability and improve overall product quality.
Documentation and Reporting
Accurate and thorough documentation is vital for maintaining consistency, ensuring compliance, and driving continuous improvement. Effective documentation and reporting practices include:
- Recording inspection results, such as defect rates, causes, and corrective actions.
- Maintaining a quality manual that outlines processes, standards, and inspection protocols.
- Using digital quality management systems (QMS) to centralize data for real-time tracking and analysis.
- Ensuring documentation is easily accessible for audits, certifications, and performance reviews.
Example: A food manufacturer might use a QMS to document temperature logs, ingredient traceability, and sanitation protocols to ensure compliance with safety regulations.
Quality Control vs. Quality Assurance: Understanding the Difference
While quality control and quality assurance (QA) share the ultimate goal of delivering superior products, there is a significant Difference between Quality Assurance and Quality Control in approach and execution. QC is centered on identifying and correcting errors post-production, while QA emphasizes error prevention through process improvement.
Quality Control (QC)
QC is a reactive strategy that ensures products align with set quality benchmarks. Key activities include:
- Conducting inspections of finished goods.
- Utilizing statistical sampling to evaluate production batches.
- Analyzing defects to uncover root causes and implement improvements.
Quality Assurance (QA)
In contrast, QA takes a preventive stance, focusing on designing processes that yield high-quality outcomes. By employing tools such as control charts and Pareto analysis, QA integrates seamlessly with frameworks like Total Quality Management (TQM) and Six Sigma. QA is Crucial for Success in Every Industry. This approach promotes continuous process enhancement, reducing the likelihood of defects.
Learn more about : Enhancing Quality Assurance.
The Importance of Quality Control in Manufacturing
Quality control (QC) plays a pivotal role in ensuring successful manufacturing operations, serving as a safeguard against inefficiencies and errors that can ripple through an organization. Effective QC ensures that production aligns with established standards, reducing the risk of defects and costly rework. By prioritizing QC, manufacturers protect their reputation, maintain customer trust, and create a foundation for sustainable growth.
The Consequences of Neglecting Quality Control
Failing to implement robust QC measures can have severe repercussions. Increased scrap rates waste valuable resources, while reworking defective products inflates production costs and consumes labor hours. Moreover, supply chain disruptions stemming from poor QC can delay deliveries, tarnish relationships with suppliers, and harm customer satisfaction. Ultimately, repeated quality issues can damage a brand’s reputation and result in lost market share.
Key Benefits of Quality Control
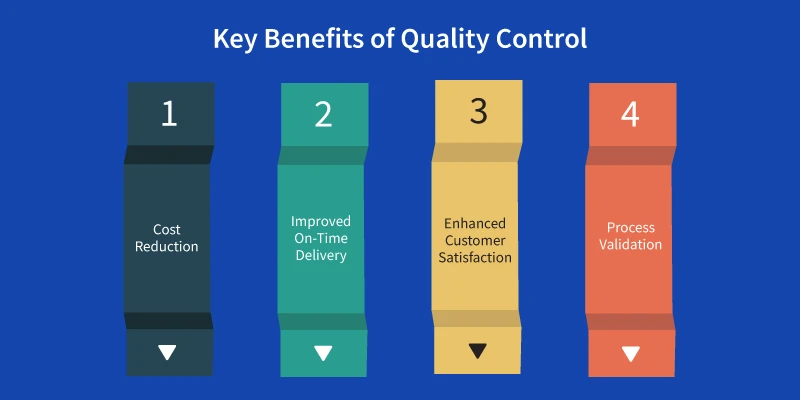
- Cost Reduction: QC minimizes waste and detects defects early, preventing costly rework or recalls. For example, implementing automated quality checks reduces human error and enhances resource efficiency.
- Improved On-Time Delivery: Effective QC streamlines production processes, ensuring that components meet standards without delays. This helps manufacturers meet tight deadlines and maintain a reliable supply chain.
- Enhanced Customer Satisfaction: Delivering consistent, high-quality products fosters customer loyalty and drives repeat purchases. Studies show that customers are more likely to recommend brands they trust for quality.
- Process Validation: QC helps identify bottlenecks and inefficiencies in production workflows. By leveraging methodologies like Lean and Six Sigma, manufacturers can refine operations, reduce downtime, and boost productivity.
Building Long-Term Success
Beyond immediate benefits, quality control contributes to long-term success by establishing a culture of excellence. Integrating QC into all levels of production ensures that quality becomes a shared responsibility, leading to consistent improvements and a competitive edge in the marketplace.
Proven Methods for Quality Control in Manufacturing
Manufacturers employ diverse QC methods to ensure product excellence. Each approach is tailored to specific requirements, industries, and production environments.
Just-in-Time (JIT) Quality Control
JIT focuses on delivering materials and components precisely when they’re needed, minimizing inventory costs and storage requirements. To support this system, stringent quality control ensures that incoming materials adhere to specifications, preventing disruptions in production. JIT demands close collaboration with suppliers and reliable QC practices to maintain seamless workflows and avoid delays caused by defective materials.
Workstation-Level Quality Control
This method involves operators inspecting components at individual workstations before passing them along the production line. Common in high-precision industries like aerospace or electronics, it ensures that any issues are caught and corrected early. This proactive approach reduces the risk of compounded defects, saves time and resources, and ensures consistent output quality at every stage of production.
Statistical Quality Control (SQC)
SQC uses statistical methods to monitor and control production quality. Random samples from production batches are analyzed to detect trends, variations, or defects. This proactive approach allows manufacturers to address potential problems before they escalate. Particularly effective in process industries like pharmaceuticals or chemicals, SQC ensures that production remains consistent and meets regulatory standards.
Inspection-Based Quality Control
Inspection-based QC focuses on evaluating finished goods to ensure they meet the required specifications. While effective at detecting nonconforming products, this method is reactive and relies heavily on addressing upstream process flaws to reduce defects. Industries such as textiles and consumer goods often use this approach to provide final quality assurance and minimize customer dissatisfaction.
Total Quality Management (TQM)
TQM is a holistic approach to embedding quality into the fabric of an organization. Research claims that; “Total quality management (TQM) is a revolutionary approach to effective management”. It encourages a culture of continuous improvement, empowering employees to identify and resolve issues at every level. By aligning organizational goals with quality objectives, TQM drives efficiency, customer satisfaction, and long-term success. This method integrates seamlessly with tools like Six Sigma for sustained improvement.
Table: Comparison of Quality Control Methods
Method | Advantages | Challenges |
---|---|---|
JIT | Minimizes inventory costs | Requires strict vendor QC |
Workstation-Level | Early defect detection | Relies on skilled operators |
Statistical QC | Trend identification and proactive fixes | Dependent on consistent production |
Inspection-Based | Final product assurance | Reactive; may miss upstream issues |
TQM | Holistic quality improvement | Requires cultural and organizational buy-in |
Best Practices for Quality Control in Manufacturing
Incorporating best practices into your quality control (QC) strategy can dramatically enhance product consistency and operational efficiency. Here are some key practices to optimize your QC efforts:
- Regular Audits Stay proactive with audits. Regular internal and external audits help spot process gaps, inefficiencies, and areas for improvement. They ensure that your production consistently meets industry standards and internal benchmarks, keeping quality at the forefront.
- Supplier Collaboration Quality starts with your suppliers. By working closely with suppliers to define and monitor material quality requirements, you prevent raw material defects from impacting final product quality. Joint efforts also help in innovating new material sourcing techniques that can improve overall production quality.
- Leveraging Technology Let technology do the heavy lifting. Automated inspection tools, such as sensors and vision systems, allow for real-time monitoring, eliminating human error. Using advanced analytics helps track performance, spot issues early, and improve product quality with minimal delays.
- Feedback Loops Listen to your team and customers. Feedback from employees on the shop floor can highlight recurring production issues, while customer insights help you understand how products perform in real-world conditions. These feedback channels drive continuous improvement, ensuring your QC process evolves with customer needs.
Incorporating these strategies not only improves product quality but also fosters a culture of constant improvement and innovation in manufacturing.
Leveraging Data for Quality Control Improvement
The integration of data-driven technologies is revolutionizing quality control. By analyzing real-time data, manufacturers can:
- Predict and prevent potential defects.
- Optimize machine performance to minimize downtime.
- Maintain consistent compliance with quality standards.
Steps for Effective Data Collection
- Process Auditing: Conduct regular audits to evaluate production performance and identify improvement areas.
- Automated Data Collection: Utilize modern systems to gather real-time data, improving accuracy and responsiveness.
- Machine Data Platforms: Leverage platforms like MachineMetrics for seamless data integration, advanced analytics, and actionable insights.
Elevate Your Manufacturing Standards with AMREP Mexico!
Quality control is a strategic advantage in today’s competitive market. Implementing robust QC measures and leveraging data insights can lead to unparalleled operational excellence and customer satisfaction.
AMREP Mexico offers specialized Quality Management services tailored to your manufacturing needs. From optimizing processes to reducing waste, our expertise ensures you achieve consistent, high-quality results.
Ready to revolutionize your manufacturing processes? Connect with AMREP Mexico today and set new benchmarks for excellence!