Proven Quality Control Methods To Ensure Excellence
Quality control (QC) is the cornerstone of operational success across industries, ensuring that products and services meet stringent standards of excellence. Whether in manufacturing, healthcare, automotive, or aerospace, effective QC processes drive customer satisfaction, minimize defects, and solidify a company’s reputation. This comprehensive guide explores quality control methods, their applications, and strategies to optimize QC processes, making it an indispensable resource for professionals and businesses striving for excellence.
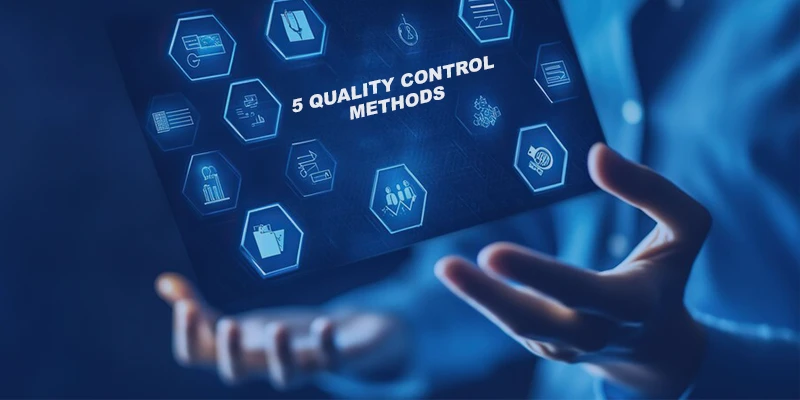
What Is Quality Control?
Quality control is a systematic approach to ensuring products or services comply with predetermined standards. QC professionals oversee processes to maintain consistency, identify defects, and improve customer satisfaction. Each industry adopts unique QC techniques tailored to its needs:
- Pharmaceuticals: Employ chemical and microbiological testing to ensure safety and efficacy.
- Automotive manufacturing: Focus on component precision and compliance with safety regulations.
In many cases, QC is considered a subset of QA. But it is to be remembered that Quality Assurance and Quality Improvement are different terms as Quality Control & Quality Inspection are.
5 Quality Control Methods
Here are the most widely used quality control methods, their principles, and how to implement them effectively.
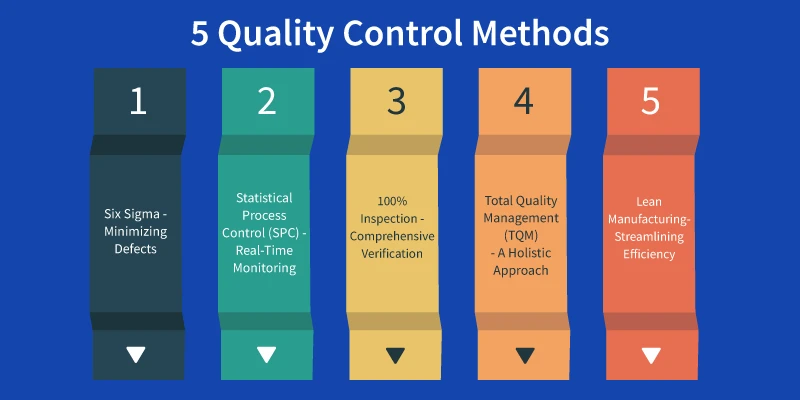
1. Six Sigma - Minimizing Defects
Six Sigma is a data-driven methodology designed to reduce defects and variability in processes. It achieves this by adhering to a structured framework known as DMAIC—Define, Measure, Analyze, Improve, and Control.
Phases Of Six Sigma:
- Define: Pinpoint the problem area and establish clear goals based on customer expectations.
- Measure: Gather quantifiable data to assess current performance levels.
- Analyze: Use statistical tools ( such as six sigma tools) to identify root causes of defects or inefficiencies.
- Improve: Develop tailored solutions to eliminate identified issues.
- Control: Establish controls to maintain improvements over time, including regular monitoring and adjustments.
Applications:
Six Sigma is a particularly effective technique of Quality control in industries like manufacturing, where precision is paramount. Companies like General Electric and Motorola have reaped immense benefits, saving billions of dollars and enhancing operational efficiency. Young Hoon Kwak claims in his research article Benefits, obstacles, and future of six sigma approach, that;
“In the 1980s, applications of the Six Sigma methods allowed many organizations to sustain their competitive advantage by integrating their knowledge of the process with statistics, engineering, and project management.“
Challenges:
While Six Sigma’s benefits are profound, its implementation requires significant training and cultural buy-in, making it resource-intensive for smaller businesses.
2. Statistical Process Control (SPC) - Real-Time Monitoring
SPC is a proactive quality control method that uses statistical techniques to monitor and control processes in real-time.By identifying deviations from standard performance, it helps prevent defects before they occur. John Oakland defines SPC in his book as;
“Statistical Process Control (SPC) is a tool that measures and achieves quality control, providing managers from a wide range of industries with the ability to take appropriate actions for business success.”
Key Components:
- Control Charts Graphical tools that track process behavior over time.
- Critical Metrics: Metrics like cycle time, defect rates, or throughput are continuously monitored.
- Data Analysis: Trends and patterns are analyzed to detect anomalies.
Implementation Steps:
- Identify key processes and define critical quality metrics.
- Collect data at regular intervals during production.
- Create control charts to visualize performance.
- Train teams to interpret charts and take corrective actions when needed.
Benefits:
- Reduces waste by addressing issues early.
- Enhances process stability, leading to consistent quality.
Applications:
SPC is commonly used techniques of Quality Contro in industries like automotive and electronics, where real-time precision is critical to operational success.
3. 100% Inspection - Comprehensive Verification
100% Inspection involves examining every single product to ensure it meets predefined quality standards. This method is particularly crucial in industries like healthcare and aerospace, where safety and reliability are non-negotiable.
Best Practices:
- Clear Criteria: Establish detailed inspection protocols to minimize ambiguity.
- Automation Tools: Utilize advanced technologies like vision systems and robotics for precision.
- Record Keeping: Maintain meticulous documentation for compliance and traceability.
Advantages:
- Offers the highest quality assurance.
- This technique of Quality Control identifies and eliminates defective products before they reach customers.
Challenges:
The resource-intensive nature of 100% inspection makes it impractical for large-scale operations. However, its application in high-stakes industries justifies the investment.
4. Total Quality Management (TQM) - A Holistic Approach
TQM emphasizes embedding quality into every aspect of an organization. Research claims that; “Total quality management (TQM) is a revolutionary approach to effective management”. This comprehensive approach fosters a culture where all employees take ownership of quality improvement.
Core Principles:
- Customer Focus: Align processes with customer expectations.
- Employee Involvement: Encourage active participation and ownership from all levels of staff.
- Continuous Improvement: Regularly refine processes based on performance data.
Implementation Tips:
- Establish cross-functional teams to address quality challenges.
- Regularly collect and analyze customer feedback. This is one of the Best Practices for Implementing TQM.
- Invest in employee development through training programs.
Advantages:
TQM promotes long-term improvements and fosters a collaborative environment, making it particularly effective for service industries and large organizations.
5. Lean Manufacturing - Streamlining Efficiency
Lean Manufacturing focuses on eliminating waste while maintaining high quality. Often used in conjunction with Six Sigma, this method prioritizes efficiency and resource optimization.
R. Sundar in his research A Review on Lean Manufacturing Implementation Techniques says that;
“The concept of lean manufacturing was developed for maximizing the resource utilization through minimization of waste, later on, lean was formulated in response to the fluctuating and competitive business environment.”
Steps to Implement Lean:
- Map Workflows: Visualize processes to identify inefficiencies.
- Value Stream Mapping (VSM): Highlight value-adding and non-value-adding activities.
- Kaizen Events: Conduct focused improvement sessions to address specific issues.
- Empower Teams: Enable employees to suggest and implement changes.
Applications:
Lean principles are widely applied in manufacturing, healthcare, and even software development, where minimizing delays and waste is critical.
Types of Quality Control Methods
Quality control methods fall into two broad categories: statistical and non-statistical techniques. The right method depends on the industry, product type, and company needs.
Statistical Quality Control (SQC) Methods:
- Control Charts: Visual tools used to monitor the stability of processes over time.
- Acceptance Sampling: A method where a random sample from a batch is tested to determine if the whole batch meets quality standards.
- Process Capability Analysis: Measures the ability of a process to produce items within set limits.
Non-Statistical Quality Control Methods:
- Inspection: Physical checks of finished products to ensure they meet quality criteria.
- Checklists: Structured lists used to ensure no step or detail is overlooked.
- Audits: Regular reviews of processes to identify inefficiencies and ensure standards are being met.
Examples of Non-Statistical Methods:
- Failure Mode and Effects Analysis (FMEA): Identifies potential failure modes in a process and evaluates their impact.
- Design of Experiments (DOE): Helps identify critical factors that affect product or process quality.
- Root Cause Analysis (RCA): A method used to identify and resolve the underlying causes of defects.
Enhancing Quality Control Processes
Continuous improvement is the cornerstone of successful quality control. To achieve excellence, businesses must adopt proactive and strategic approaches tailored to their unique needs. Here are key strategies to elevate QC practices:
Leverage Data Analytics
Modern technology enables companies to harness the power of data to refine their QC processes:
- Predictive Analytics: By analyzing historical data, organizations can identify trends and anticipate potential quality issues before they occur.
- Real-Time Dashboards: Interactive dashboards allow for continuous monitoring of quality metrics, enabling quick identification of anomalies and immediate corrective actions.
These tools not only enhance decision-making but also minimize defects and optimize operational efficiency.
Emphasize Training and Certification
Equipping employees with the right skills ensures they contribute effectively to QC initiatives:
- Certifications: Encourage employees to obtain recognized credentials like Six Sigma Green Belt, Black Belt, or ISO certification, which enhance their understanding of quality management principles.
- Workshops: Conduct regular training sessions to keep teams informed about emerging trends, technologies, and best practices in quality control.
Well-trained employees are more likely to identify and address quality issues effectively, ensuring long-term success.
Foster Effective Communication
Transparent and efficient communication channels are critical for seamless quality management:
- Feedback Mechanisms: Create systems that enable employees to share insights and report concerns without hesitation.
- Cross-Department Collaboration: Promote interdepartmental communication to align quality goals and address issues collaboratively.
Clear communication fosters accountability and ensures that quality standards are consistently upheld.
Stay Compliant and Updated
Adhering to regulations and staying informed about advancements in quality control is essential:
- Regulatory Changes: Monitor updates to industry-specific regulations and ensure compliance through regular audits and process reviews.
- Emerging Technologies: Stay ahead by integrating new tools and methods like artificial intelligence or advanced robotics into QC practices.
These measures help businesses maintain competitive standards and protect their reputation.
Quality Control Applications Across Industries
Quality control is integral across various sectors, with tailored methods ensuring specific requirements are met:
Industry | Key QC Methods | Example Applications |
---|---|---|
Manufacturing | SPC, Lean Six Sigma | Assembly line defect reduction |
Automotive | 100% Inspection, SPC | Ensuring parts meet safety standards |
Healthcare | TQM, 100% Inspection | Verifying medical device safety |
Food Production | Microbiological Testing | Preventing contamination |
Pharmaceuticals | Six Sigma, SPC | Ensuring drug efficacy and safety |
Each industry relies on quality control to meet stringent safety, performance, and regulatory standards. For instance, manufacturing employs SPC and Lean Six Sigma to optimize processes, while the food production sector prioritizes microbiological testing to maintain hygiene and safety. By leveraging the right QC methods, organizations across these industries ensure product reliability and customer satisfaction.
Take Your Quality Standards to the Next Level with Amrep Mexico!
Achieving consistent quality is a journey that requires dedication and expertise. At Amrep Mexico, we specialize in implementing customized quality control systems tailored to your industry. From minimizing defects to enhancing customer satisfaction, our team is committed to helping you achieve operational excellence.
Ready to transform your quality control processes? Contact us to avail reliable Quality Management services that help businesses maintain product excellence. Our expertise ensures that your products meet the highest standards, providing consistency, reliability, and customer satisfaction.