Total Quality Control (TQC): The Blueprint for Business Excellence
Quality is no longer just a department—it’s a way of life for successful organizations. Businesses that thrive in the long run aren’t just focused on producing good products; they’re committed to continuous improvement, customer satisfaction, and operational excellence across the board.
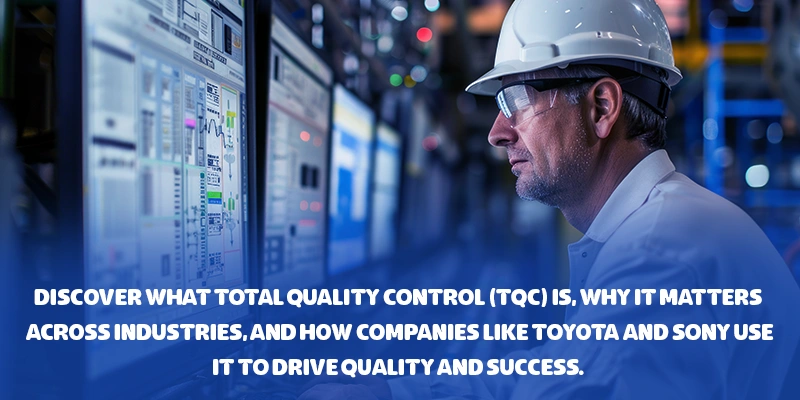
Whether you're a manufacturer, service provider, or tech startup, understanding and implementing TQC can be a game-changer. Let's dive deep into what Total Quality Control really means and how it can transform your organization.
What Is Total Quality Control?
Total Quality Control (TQC) is a comprehensive management approach that emphasizes high-quality output through every stage of production or service delivery. Unlike traditional quality control, which often inspects for defects after the fact, TQC is proactive, involving all departments and employees in maintaining and improving quality standards.
The concept was popularized in Japan in the post-World War II era, especially through the work of quality gurus like W. Edwards Deming, Joseph Juran, and Kaoru Ishikawa. Japanese companies like Toyota took these principles to heart, leading to the global success of practices such as Lean Manufacturing and Six Sigma.
Why Total Quality Control Matters—No Matter Your Industry
In manufacturing, TQC helps minimize waste, reduce defects, and streamline production workflows. Imagine a production line that not only detects problems but prevents them before they happen. That’s TQC in action.
Also read: Quality Control in Manufacturing: A Comprehensive Guide
In service-based industries like hospitality, healthcare, or finance, TQC ensures every customer interaction is smooth, consistent, and value-driven. From front-line staff to backend systems, quality becomes everyone's responsibility—not just a department’s.
And in the tech world, where innovation moves fast and customer expectations are sky-high, TQC provides a structured way to manage risk, improve user experience, and launch products with confidence. It encourages agile thinking, data-driven decisions, and a commitment to continuous improvement.
No matter the sector, the common thread is this: Total Quality Control empowers organizations to deliver value consistently and predictably—turning satisfied customers into loyal advocates.
Core Principles of Total Quality Control
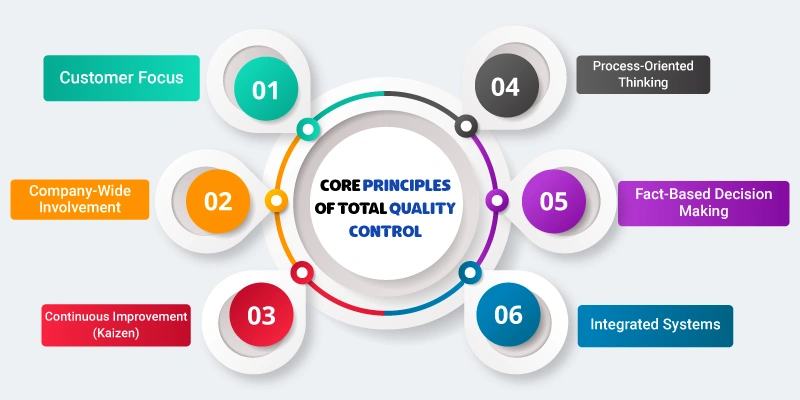
1. Customer Focus
TQC begins and ends with the customer. Meeting or exceeding customer expectations is the primary goal. Feedback loops are essential, and customer complaints are treated as opportunities for improvement.
2. Company-Wide Involvement
Quality is everyone’s job—from top executives to frontline workers. Departments like HR, finance, and marketing are just as responsible for quality as production or service teams.
3. Continuous Improvement (Kaizen)
There’s always room for improvement. TQC encourages small, incremental changes on a continuous basis, rather than relying on big, occasional overhauls.
4. Process-Oriented Thinking
Focus is placed on how work gets done. By improving processes, you improve outcomes. Tools like process mapping and root cause analysis are frequently used.
5. Fact-Based Decision Making
Decisions are made using data and statistical analysis. TQC often incorporates tools like control charts, Pareto analysis, and fishbone diagrams.
6. Integrated Systems
All departments and processes are interconnected. An issue in one area can affect the whole system, which is why a holistic view is essential.
Benefits of Total Quality Control
- ✅ Higher Customer Satisfaction
- ✅ Lower Operational Costs
- ✅ Increased Efficiency and Productivity
- ✅ Fewer Errors and Defects
- ✅ Stronger Employee Engagement
- ✅ Competitive Market Advantage
In essence, TQC can help organizations do more with less—without compromising on quality.
Key Tools & Techniques in TQC
Here are some commonly used tools in Total Quality Control initiatives:
- PDCA (Plan-Do-Check-Act) Cycle
- Ishikawa (Fishbone) Diagrams
- Pareto Charts
- Control Charts
- Flowcharts
- 5S Methodology
- Benchmarking
These tools help in analyzing problems, monitoring progress, and ensuring quality standards are maintained.
Read More: How to Become a Quality Control Inspector
Challenges in Implementing TQC
While TQC offers numerous benefits, it also comes with some challenges:
- Cultural Resistance: Shifting mindsets and behaviors can be tough.
- Training Requirements: Staff need proper training to understand and use TQC tools.
- Time and Investment: It’s not a quick fix; TQC takes time, commitment, and leadership.
- Consistency: Quality control needs to be sustained, not just introduced.
Real-World Examples of TQC Success
Toyota: Redefining Manufacturing Through TQC
Toyota is often held up as the gold standard when it comes to quality and efficiency in manufacturing. Their version of TQC is deeply embedded in what is now famously known as the
Toyota Production System (TPS). This system emphasizes continuous improvement (Kaizen), respect for people, and elimination of waste (Muda).
TQC was a cornerstone in shaping this philosophy. Instead of relying on post-production inspection, Toyota integrated quality at every step—from supplier relationships and raw materials to the final assembly line. Workers are trained to stop the production line when they notice a defect (a concept called jidoka), empowering them to take ownership of quality. This proactive approach not only reduced defects but also significantly boosted productivity and customer satisfaction, making Toyota a global leader in the automotive industry.
Sony: Innovation Meets Quality
Sony’s rise to global prominence was not just due to groundbreaking innovation but also because of its deep commitment to quality through TQC. After World War II, Sony was one of the early Japanese companies to adopt TQC principles, influenced by quality pioneers like W. Edwards Deming and Joseph Juran.
Sony built its reputation by ensuring quality was a company-wide responsibility, not just the job of engineers. From the iconic Walkman to high-definition TVs and gaming consoles, Sony embedded TQC into every stage of product development and customer experience. Employees were encouraged to provide suggestions for improvement, and cross-functional teams were formed to resolve quality issues collaboratively.
This emphasis on high standards helped Sony maintain its brand value and consumer trust for decades, especially in an industry where product life cycles are short and competition is fierce.
Motorola: Pioneering TQC and Six Sigma
Motorola’s commitment to quality didn’t just improve their operations—it sparked a global movement. In the 1980s, Motorola was facing increasing competition from Japanese electronics firms. In response, they invested heavily in Total Quality Control and eventually developed Six Sigma, a data-driven methodology aimed at reducing defects to near perfection.
The company trained thousands of employees in quality management techniques, aligned goals across departments, and used real-time data to solve problems at their root cause. As a result, Motorola reportedly saved billions of dollars by reducing variation and improving product reliability.
Their efforts were so successful that in 1988, Motorola became one of the first recipients of the prestigious Malcolm Baldrige National Quality Award in the U.S.—a testament to how deeply TQC had transformed their operations and culture.
TQC in the Age of AI and Automation
Automation and artificial intelligence are revolutionizing industries, from manufacturing and logistics to customer service and healthcare. But even in these high-tech environments, the need for Total Quality Control hasn’t diminished—it’s become even more essential.
AI systems are only as good as the data they are trained on and the processes they support. TQC ensures that these systems are implemented with a strong foundation of quality assurance, risk management, and continuous monitoring. Whether it’s predictive maintenance in smart factories or algorithmic decision-making in finance, TQC provides the structure needed to ensure reliability, transparency, and ethical accountability in automated systems.
In a world where machines make decisions, TQC ensures those decisions are right.
Demystifying TQC Myths
Many modern businesses—especially startups and SMEs—believe TQC is only for large-scale manufacturers or multinational corporations. Others assume it’s too rigid, too complex, or outdated in today's agile work culture.
Let’s bust those myths.
TQC is not a one-size-fits-all checklist. It’s a customizable framework that emphasizes quality at every level and can be tailored to suit a business of any size or industry. In fact, small businesses that adopt TQC principles often outperform their competitors in consistency, customer satisfaction, and operational efficiency.
TQC isn't about adding bureaucracy—it's about removing friction and waste while building better products, services, and teams.
Is Your Business Ready for TQC?
Total Quality Control isn’t just a strategy—it’s a philosophy. It requires commitment from every level of an organization and a culture that doesn’t just tolerate change but actively seeks it out. If your business is looking to scale, innovate, and dominate in your market, TQC isn’t just an option—it’s a necessity.
Want to get started with Total Quality Control in your organization?
Let’s chat! Whether you need help training your team or auditing your processes, building a culture of quality starts with that first step.
At AMREP Mexico, we specialize in helping manufacturers and suppliers implement robust quality systems that drive performance and exceed customer expectations. With decades of experience in quality engineering, supplier audits, andinspection services , we’re here to be your partner in excellence.
Contact us to learn how our solutions can help you build a culture of quality from the ground up.