Four Main Types of Quality Inspection
Quality inspection is a critical component of any successful production process. In manufacturing consumer goods, electronics, or industrial equipment, implementing effective quality control measures is essential to maintain consistency and minimize defects.
In this blog, we’ll explore each type of quality inspection and its role in delivering top-tier products to your customers.
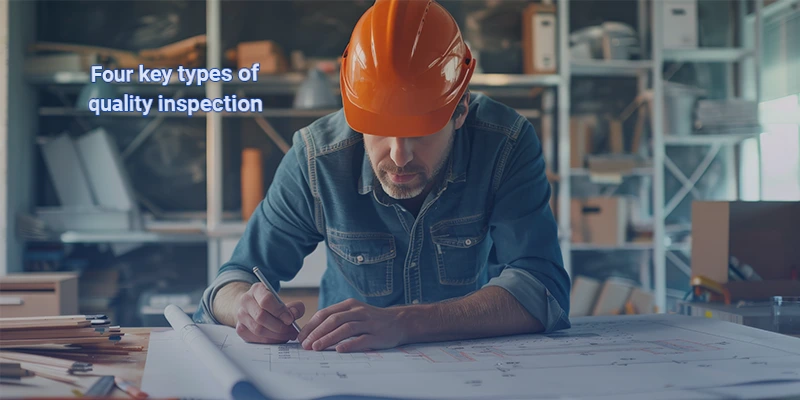
What is Quality Control?
Quality control is a systematic process used to ensure that a product meets the required quality standards set by the company or regulatory authorities. It involves testing, inspecting, and certifying products at various stages of production, from raw materials to finished goods.
A well-structured quality control system allows businesses to identify potential issues early in the process, enabling proactive corrective measures to be taken. This not only helps in delivering customer satisfaction but also plays a key role in achieving a zero-waste supply chain by minimizing defects and inefficiencies. Quality control inspectors conduct thorough tests throughout production to ensure that the final product meets or exceeds all expectations.
What are the 4 Types of Quality Inspection?
Four main types of quality inspections include—Pre-Production Inspection, During Production Inspection, Pre-Shipment Inspection, and Container Loading/Unloading Inspections. These help businesses to maintain product quality and streamline the supply chain. Depending on your product and relationship with the supplier, one or more of these inspections may be needed.
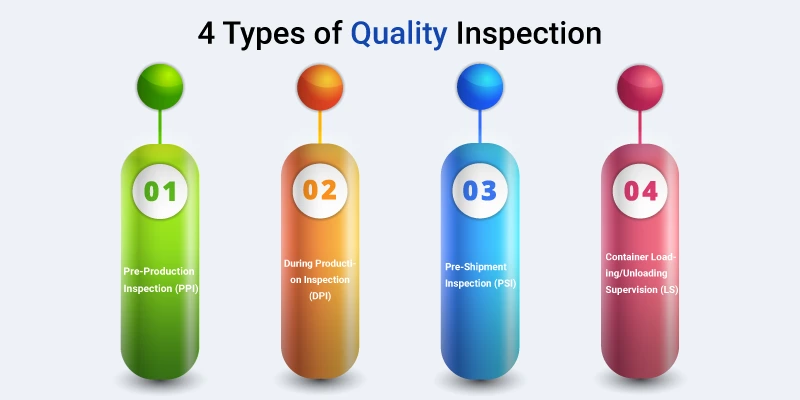
1. Pre-Production Inspection (PPI)
A Pre-Production Inspection (PPI) takes place before production begins. Its primary purpose is to assess the quality and quantity of raw materials and components, ensuring that they align with the product specifications.
This inspection is particularly useful when working with a new supplier or handling large contracts with strict delivery deadlines. A PPI helps set clear expectations regarding production timelines, shipping dates, and quality standards, reducing the chance of miscommunication. It’s an effective way to prevent delays and ensure that the production process runs smoothly from the outset.
Pre-Production Inspection (PPI) Includes:
Pre-Production Inspection (PPI) is conducted before the actual manufacturing process begins. It aims to ensure that all materials, components, and other essential factors are ready and meet the required standards. Here’s what typically falls under a PPI:
- Raw Materials and Components Check
- Supplier Capability Assessment
- Quality Control Systems Review
- Production Planning Verification
- Product Sample Review
- Packaging and Labeling Inspection
- Compliance and Regulatory Checks
2. During Production Inspection (DPI)
During Production Inspection (DPI), also known as DUPRO (During Production Inspection), occurs while the production process is in progress. This inspection type is useful for products that are continuously manufactured or when earlier inspections, like a PPI, have identified potential issues.
DPI is usually conducted when only 10-15% of the order is complete. Inspectors check for any quality deviations and provide feedback to ensure that corrective actions are taken early. This proactive approach helps identify and fix issues before they escalate, saving time, reducing rework, and ensuring that product specifications are being met throughout production.
During Production Inspection (DPI) Includes:
During Production Inspection (DPI), also known as DUPRO (During Production Inspection), is conducted while manufacturing is still underway. Here's what typically falls under a DPI:
- Product Quality Check
- Sampling of Finished Units
- Verification of Specifications
- Production Process Monitoring
- Checking for Defects and Rework
- Compliance with Safety and Regulatory Standards
- Inventory and Material Control
- Packaging and Labeling Check
3. Pre-Shipment Inspection (PSI)
Pre-Shipment Inspection (PSI) occurs once production is finished and products are ready for shipment. It is a vital step to confirm that the products meet the buyer's specifications before they are shipped.
This inspection typically takes place when at least 80% of the goods are packed for shipping. A random sample of products is selected for a thorough inspection, checking for defects and verifying that the products meet the agreed standards. PSI is crucial in preventing the shipment of faulty products and ensuring that the goods conform to the buyer’s quality requirements.
Pre-Shipment Inspection (PSI) is performed on finished products just before they are shipped to the customer. The goal of PSI is to ensure that the goods meet the buyer’s specifications and quality standards, preventing the shipment of defective or incorrect products. Here’s what is typically included in a PSI:
- Product Sampling
- Visual Inspection
- Functional Testing
- Measurement and Specification Check
- Packaging Inspection
- Quantity Verification
- Compliance with Safety and Regulatory Standards
- Inspection Report and Certification
- Defect Identification and Corrective Action
4. Container Loading/Unloading Supervision (LS)
Container Loading/Unloading Supervision is a final inspection step that ensures products are safely loaded into and unloaded from shipping containers. This process guarantees that the products are handled correctly throughout their journey.
Inspectors oversee the entire loading or unloading process to ensure that products are packaged properly and that the shipping container is in good condition. They also verify that the quantities and product details match the order and that the packaging complies with specifications. This inspection ensures that products arrive at their destination in optimal condition.
Container Loading/Unloading Supervision (LS) Includes:
Container Loading and Unloading Supervision (LS) is a crucial quality control step that ensures products are safely and correctly loaded into and unloaded from shipping containers. This inspection helps prevent damage during transport and ensures that the products reach their destination in the same condition as they left the factory. Here’s what typically falls under Container Loading/Unloading Supervision:
- Verification of Product Quantity
- Inspection of Packaging and Labeling
- Loading Process Monitoring
- Condition of the Shipping Container
- Seal and Documentation Check
- Unloading Supervision
- Ensuring Compliance with Safety Standards
- Damage or Loss Reporting
- Final Inspection Report
Piece-by-Piece Inspections
In addition to these four main types, there is a more detailed procedure known as Piece-by-Piece Inspection. This inspection involves checking every individual product to assess appearance, workmanship, function, and safety.
This type of inspection is typically used for high-value or critical products that require strict compliance with specifications. It is usually performed before or after the packaging inspection. Once the products pass this inspection, they are sealed and certified to confirm that they meet the required quality standards. Piece-by-Piece Inspection ensures complete compliance, making it suitable for industries where every item must be flawless.
Read More: Proven Quality Control Methods
8 Reasons Why Quality Inspection is Crucial for Your Business
Quality inspection delivers exceptional products and maintains operational excellence. Here’s why it’s so important:
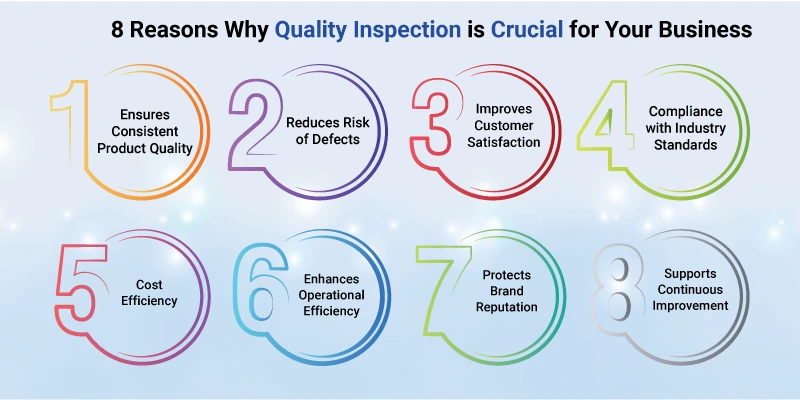
1. Ensures Consistent Product Quality
Quality inspection guarantees that every product meets the required standards, ensuring consistency in quality and performance. This helps build trust with customers and enhances your brand’s reputation.
2. Reduces Risk of Defects
By identifying defects early in the production process, quality inspections prevent defective products from reaching the market. This reduces the risk of costly recalls and customer dissatisfaction.
3. Improves Customer Satisfaction
Delivering high-quality products that meet customer expectations leads to better customer satisfaction and loyalty. Satisfied customers are more likely to become repeat buyers and recommend your products to others.
4. Compliance with Industry Standards
Quality inspections ensure that your products meet industry regulations and standards, avoiding legal issues and fines. Compliance is critical in sectors like food, pharmaceuticals, and electronics, where safety and quality are non-negotiable.
5. Cost Efficiency
By catching issues early, quality inspection helps prevent rework, wastage, and additional costs associated with defective products. It ultimately saves money in the long run by improving the efficiency of the production process.
6. Enhances Operational Efficiency
Regular quality checks identify areas for improvement in the manufacturing process, streamlining operations and reducing bottlenecks. This leads to higher productivity and smoother workflows.
7. Protects Brand Reputation
Consistently delivering high-quality products helps strengthen your brand image and protect your reputation in the market. A good reputation can significantly impact customer retention and attract new business opportunities.
8. Supports Continuous Improvement
Quality inspections provide valuable feedback that can be used to improve processes, techniques, and materials. Continuous monitoring helps maintain high standards and fosters innovation in production.
Why AMREP is a Perfect Choice for Your Quality Control Needs
Four types of quality inspection—Incoming Material Inspection, In-Process Inspection, Final Product Inspection, and Packaging & Shipping Inspection—ensures that your products meet the highest standards of quality, consistency, and compliance.
At AMREP Mexico, we are committed to delivering top-notch quality control solutions tailored to your specific needs. With our effective Supplier Management Solutions, you can trust us to help you maintain the highest quality standards throughout your production process. Our comprehensive approach ensures seamless coordination with suppliers, fostering stronger relationships and consistent product quality. Let us be your partner in achieving excellence, every step of the way.