Quality Control - What Is It And How It Works?
Quality control (QC) is not merely a process—it is a mindset. Every product that reaches the consumer has undergone a series of meticulous tests, inspections, and measures to ensure it meets a predefined standard of excellence.
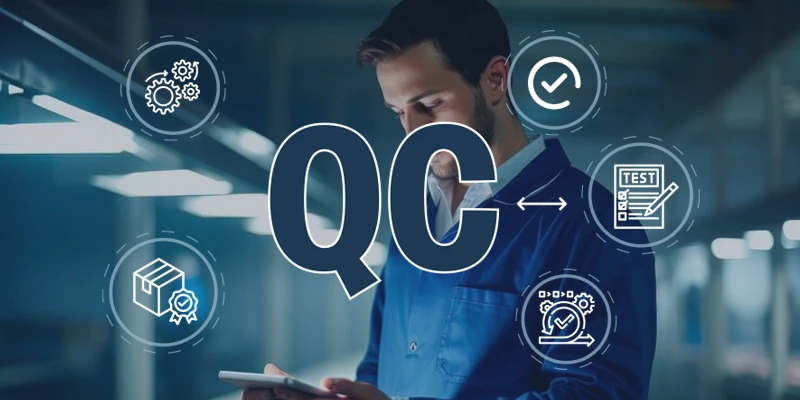
As highlighted by W.A. Shewhart in his seminal 1926 study published inThe Bell System Technical Journal:
“Variations in product quality are inevitable due to random fluctuations in environmental and human factors. However, through systematic control measures, manufacturers can produce products that are consistent and reliable, achieving excellence by minimizing non-assignable causes of variation.”
Whether it's a food product, an aircraft, or a piece of software, quality control is the backbone of industry standards and customer satisfaction. Let’s take a deeper look at QC, exploring its core principles, key methods, best practices, industry-specific strategies, and the vital role it plays in modern manufacturing and service sectors.
What Is Quality Control (QC)?
“Quality Control (QC) is the systematic process employed by businesses to ensure that products and services consistently meet or exceed predefined quality standards.”
A scholarlydefinition of Quality says that:
“We engage in quality control in order to manufacture products with the quality which can satisfy the requirements of Consumers. The mere fact of- meeting national standards or specifications is not the answer. It Is simply insufficient.”
It's not just about checking whether a product is good enough—it’s a comprehensive approach that emphasizes precision, consistency, and safety across every step of production and service delivery. QC involves a wide range of activities, including product testing, identifying defects, setting specifications, and making necessary adjustments. At its core, QC is about creating a culture where quality is paramount, ensuring that the end product is safe, reliable, and performs as expected.
- QC is an essential process that helps maintain and improve product quality.
- It ensures customer safety and compliance with industry standards.
- Effective QC minimizes errors, leading to increased efficiency and consumer trust.
Types of Quality Control
Quality control can be broken down into several types, each addressing different aspects of the production process:
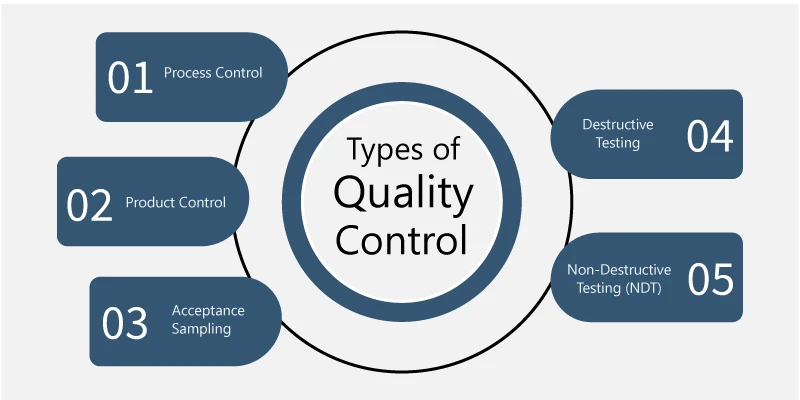
- Process Control: Involves monitoring and controlling the production process itself to ensure it stays within defined parameters. This can include temperature, pressure, and timing during manufacturing.
- Product Control: Focuses on the final product’s conformity to specifications. This can involve measuring product dimensions, weight, appearance, and performance.
- Acceptance Sampling: A statistical method used to inspect a random sample of goods rather than inspecting every single product. If the sample meets quality standards, the entire batch is accepted.
- Destructive Testing: A method used primarily for critical products (e.g., pharmaceuticals, aerospace) where the product must be tested in a way that might damage it, like crash testing for vehicles.
- Non-Destructive Testing (NDT): This method ensures that the product remains intact while being tested. Techniques include ultrasound, radiographic inspection, and eddy current testing.
The QC Process Flow:
- Defining Specifications: Setting clear, measurable standards for the product.
- Inspection: Conducting inspections at various stages of the production process.
- Reporting: Identifying and documenting any defects or deviations.
- Rectification: Making necessary adjustments or rejections.
- Validation: Final tests before shipping to confirm quality standards are met.
Table: Key Stages in the QC Process
Stage | Description |
---|---|
Raw Material Check | Ensuring materials meet required standards. |
In-Process Inspections | Continuous checks during production. |
Final Inspection | A comprehensive review of finished products. |
Post-Production Testing | Additional tests after manufacturing. |
Customer Feedback Analysis | Evaluating end-user reports for improvements. |
What does a QC do?
The Importance of Quality in Business
The slightest defect whether in manufacturing, material selection, or design can lead to far-reaching consequences, from financial losses to damage to a company’s credibility. This is where Quality Control (QC) comes in. QC is an integral part of a company's strategy to maintain product excellence, reduce risks, and protect the bottom line.
Here’s why QC is indispensable:
1. Cost Efficiency
One of the primary benefits of implementing quality control processes is cost savings. Identifying defects early in the production process or even during the design phase can significantly reduce the cost of rework, returns, or waste.
- Preventing Costly Rework: If defects are identified in the early stages of production, companies can make the necessary adjustments before the product moves forward. This prevents the need for expensive rework or even scrapping the product entirely.
- Minimizing Returns and Refunds: Products that fail to meet customer expectations are often returned, leading to costs related to shipping, restocking, and sometimes even reputational damage. QC ensures that these costly scenarios are avoided by catching issues before they reach the consumer.
Table: Cost Savings Through Effective QC
QC Stage | Potential Cost Savings |
---|---|
Raw Material Inspection | Avoids costly raw material wastage and ensures compatibility with product specs. |
In-Process Inspections | Reduces rework by identifying defects early in production. |
Final Inspection | Prevents costly returns by ensuring product quality before shipping. |
Post-Production Testing | Identifies functional defects that could result in product failure. |
2. Customer Satisfaction
When QC is embedded in the production process, customers receive products that are reliable, safe, and durable, which builds trust and loyalty.Ishikawa says that:
“the proof of high quality is the satisfaction of ever changing consumer expectations.”
QC helps businesses ensure that:
- Consistency is maintained across production: Customers expect that products purchased at different times will meet the same high standards.
- Products meet or exceed expectations: From functionality to aesthetics, QC ensures that products deliver what customers expect, making them more likely to return for future purchases.
A company that prioritizes QC demonstrates a commitment to delivering excellent products, which not only satisfies customers but also turns them into brand advocates.
Table: Customer Benefits from Quality Control
Benefit | Impact on Customer Experience |
---|---|
Product Consistency | Ensures customers always receive the same high-quality product. |
Reliability and Trust | Customers are more likely to trust and purchase again from the same brand. |
Safety Assurance | Customers feel confident that the product is safe for use. |
Positive Brand Perception | High-quality products enhance a brand’s reputation in the market. |
3. Risk Management
Effective QC systems play a crucial role in managing risks that could threaten a business. By thoroughly testing and inspecting products during the production process, companies can mitigate the likelihood of dangerous defects, safety hazards, or non-compliance with regulations.
- Product Recalls: Products that fail to meet safety standards or pose health risks may need to be recalled. This is an expensive and reputation-damaging process, but QC helps prevent safety issues before products reach consumers.
- Legal Liability: Defective products that cause injury or fail to meet safety laws can lead to lawsuits and regulatory penalties. A strong QC process ensures compliance with safety standards, reducing legal risks.
- Brand Damage: A single defective product can significantly harm a brand’s reputation. QC plays a vital role in preventing products from reaching the market that could undermine consumer trust and brand integrity.
4. Avoiding Subpar Products and Legal Repercussions
Without proper QC systems in place, businesses run the risk of delivering substandard products, which could compromise safety, function, or consumer satisfaction. The consequences of such lapses are severe and can include:
- Customer Dissatisfaction: Defective products can lead to bad reviews, reduced consumer confidence, and a drop in sales.
- Legal Repercussions: If a product fails to meet industry regulations or causes harm to consumers, the business may face lawsuits, regulatory fines, and mandatory product recalls.
- Loss of Reputation: Reputation is one of the most valuable assets a company can have. Delivering subpar products erodes consumer trust and can result in long-lasting damage that is hard to repair.
By proactively identifying and correcting potential defects, businesses not only avoid financial losses but also ensure that their products are safe and functional, protecting both the bottom line and the brand.
How QC is Integrated in the Manufacturing Process
Integrating QC into the manufacturing process is not an afterthought—it’s a continuous effort that begins at the planning phase and continues through production to the final product.
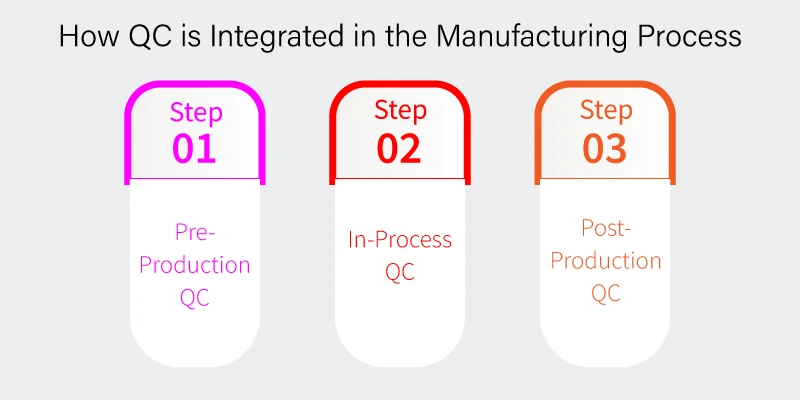
Here’s a breakdown of how QC is integrated at each stage of the manufacturing process:
1. Pre-Production QC
The pre-production phase is crucial for laying the foundation for quality assurance throughout the manufacturing process. At this stage, QC measures are put into place to ensure that both the design and sourcing decisions align with quality standards.
Design Phase:Quality control begins even before the production line starts running. During the design phase, QC teams collaborate with design engineers to ensure that the product meets both functional and quality specifications. This phase ensures that:
- Quality Standards are Integrated: Quality benchmarks are incorporated into the design process to prevent issues down the line. For example, material choices, assembly methods, and safety features are designed with QC standards in mind.
- Feasibility and Testability: The product design is evaluated for ease of testing and potential for failure during the manufacturing and usage stages. This proactive approach reduces the likelihood of errors during production.
Example: If a product is designed to be heat-resistant, the QC team will specify the required materials and testing methods to ensure the product meets these standards before production starts.
Supplier Selection:Choosing the right suppliers who meet the required quality standards is critical to ensuring that only the best materials and components enter the production process. The supplier selection process often includes:
- Supplier Audits and Assessments: QC teams audit potential suppliers to verify their ability to meet quality standards consistently. This can include site visits, reviewing production processes, and assessing past performance.
- Material Specifications: Clear specifications are provided to suppliers to ensure that raw materials meet the necessary standards for quality and safety. This helps prevent defects in the final product by ensuring that only high-quality materials are used from the start.
Table : Key Pre-Production QC Activities
QC Activity | Objective | Outcome |
---|---|---|
Design Review | Integrating quality standards into product design. | Minimizes future design flaws and issues. |
Supplier Audits | Verifying supplier reliability and material quality. | Ensures raw materials meet product standards. |
Material Specifications | Setting clear material requirements for suppliers. | Reduces the risk of poor-quality inputs. |
2. In-Process QC
Once production begins, in-process QC ensures that the product is consistently manufactured to meet quality standards throughout each stage. This phase is essential to monitor and control quality in real time, allowing for immediate adjustments if any deviations occur.
Material Inspection:
Before production begins, the raw materials are inspected for compliance with specifications. This inspection ensures that the materials are free from defects, meet safety standards, and are suitable for use in the manufacturing process.
- Visual and Functional Inspections: QC teams check the raw materials for visible defects, such as cracks, discoloration, or damage. Additionally, they test materials for functional properties such as strength, flexibility, or conductivity.
- Supplier Traceability: For materials that come from external suppliers, traceability is crucial to ensure that any issues can be traced back to the source.
Process Control:
During the manufacturing process, QC teams regularly monitor various factors to ensure that the production environment remains within acceptable limits. Process control involves:
- Real-Time Monitoring: QC teams monitor parameters such as temperature, pressure, and machine calibration to ensure consistency and prevent deviations from specifications.
- Statistical Process Control (SPC): This technique uses statistical methods to monitor and control the manufacturing process. By collecting data and analyzing trends, manufacturers can detect problems early and make adjustments before defects occur.
Example: In an automated assembly line, if a machine's tolerance starts to drift outside of acceptable limits, the system may flag the issue in real-time, allowing for corrective action.
Table: In-Process QC Monitoring Methods
Monitoring Method | Purpose | Example |
---|---|---|
Material Inspection | Ensures incoming materials meet required standards. | Testing raw materials for defects or non-conformance. |
Real-Time Monitoring | Continuously checks process parameters to maintain consistency. | Monitoring temperature and speed during production. |
Statistical Process Control (SPC) | Uses data to track process performance and identify issues. | Analyzing production data to detect trends. |
3. Post-Production QC
After manufacturing is complete, the focus shifts to ensuring that the final product meets the established quality standards before it is packaged and shipped. Post-production QC activities include detailed inspections and additional testing to catch any remaining defects.
Final Inspection:
Final inspection is the last step before products are packaged and shipped to customers. It involves a comprehensive review of the finished products to ensure they are free from defects and meet all necessary specifications. QC teams will:
- Visual and Functional Checks: Each product is thoroughly inspected for any visible defects such as scratches, cracks, or incorrect labels. Functional testing ensures that the product operates as intended.
- Dimensional Verification: QC teams measure the product to ensure that it meets the specified dimensions and tolerances.
Example: In electronics manufacturing, the final inspection would include testing the device's performance, battery life, and screen resolution to ensure they meet product specifications.
End-User Testing:
In some industries, products undergo additional testing in real-world conditions to verify their reliability and performance. This testing phase can involve:
- Simulated Usage Tests: Products are tested in conditions that closely resemble actual use to assess their durability and performance under stress.
- Customer Feedback Integration: Testing may also involve reviewing customer feedback from product trials or beta testing to identify any potential issues.
Table: Post-Production QC Activities
QC Activity | Objective | Outcome |
---|---|---|
Final Inspection | Ensuring products meet quality standards before shipping. | Verifies that finished products are defect-free. |
End-User Testing | Verifying product performance in real-world conditions. | Identifies potential user-experience issues. |
How Quality Control Is Implemented Across Industries
Every industry uses QC differently depending on the nature of the product and its intended purpose. Here's how QC looks in different sectors:
- Foundation First: QC prevents contamination or harmful chemicals from entering the food supply. Rigorous testing ensures that food products are safe and meet health standards.
- Automotive Manufacturing: QC ensures that car parts, such as engines and transmissions, function smoothly and meet design specifications, preventing safety issues.
- Electronics Manufacturing: QC involves using meters and stress tests to ensure that all parts of a gadget function optimally and safely under varying conditions.
- Aerospace: QC is crucial in aerospace. Manufacturers must track, inspect, and re-inspect all items, maintaining rigorous standards to prevent failures during flight.
By adjusting their QC methods to suit the specific requirements of their products, businesses can safeguard both their operations and their customers.
What is the difference between QA and QC?
Quality Control vs. Quality Assurance:
Although “Quality Control” and “Quality Assurance” are often used interchangeably, they focus on different aspects of quality management:
- Quality Control (QC) focuses specifically on testing and inspecting products during and after production to ensure they meet standards.
- Quality Assurance (QA) is a broader process that encompasses all activities designed to ensure the overall quality of products, including designing processes that prevent defects before they happen.
Aspect | Quality Control (QC) | Quality Assurance (QA) |
---|---|---|
Focus | Focuses on inspecting and testing products. | Focuses on improving and optimizing production processes. |
Stage of Application | Applied during and after production to verify the final product. | Applied throughout the entire production process to prevent defects. |
Goal | Detect defects or deviations from quality standards. | Prevent defects by ensuring optimized processes and standards. |
Scope | Product-specific inspections and testing. | Broad, involving process design, training, and system improvements. |
Method | Involves activities like material testing, inspections, and evaluations. | Involves designing processes, risk management, and supplier evaluation. |
Action | Corrects products that do not meet standards. | Ensures processes are effective to prevent defects. |
Outcome | Ensures the product meets predefined quality criteria. | Ensures overall product quality through optimized production processes. |
In many cases, QC is a subset of QA. QA programs ensure that every part of the production process is optimized for quality, while QC verifies that the final product meets all defined standards. Quality Assurance and Quality Improvement are also different terms asQuality Control & Quality Inspection.
Proven QC Methods for Consistent Excellence
Maintaining consistent product quality requires the use of proven methods and techniques to identify deviations and correct them before they affect the final product. Here are a few commonly used quality control methods:
1. X-Bar Chart
The X-bar chart is a statistical tool that tracks variations in product attributes over time. It helps companies monitor production consistency by distinguishing between random defects and systematic variations. This chart provides insights into whether a defect is an isolated incident or part of a recurring problem, allowing businesses to implement targeted corrective actions. It’s commonly used in industries where product consistency is key, such as manufacturing and food production.
Attribute | Description |
---|---|
X-Bar Chart Usage | To monitor variations in product attributes |
Purpose | To monitor variations in product attributes |
Ideal For | Industries with mass production lines |
Benefit | Identifies systematic issues early |
2. Taguchi Method
The Taguchi Method focuses on designing products and processes to minimize variations and defects, even before manufacturing begins. This approach emphasizes the importance of robust design—ensuring that products can perform consistently despite external factors such as environmental conditions. By addressing potential sources of variation in the design phase, companies can significantly reduce costs related to defects and improve overall product reliability.
Attribute | Description |
---|---|
Taguchi Method Usage | To design out defects and variations |
Purpose | To design out defects and variations |
Ideal For | High-complexity products with multiple variables |
Benefit | Cost-effective method for defect prevention |
3. 100% Inspection Method
The 100% Inspection Method involves inspecting every single product to ensure it meets the required standards. This method is commonly used for high-value or sensitive products, such as metals or electronic components, where even a small defect could lead to significant safety issues or financial loss. While it is resource-intensive, the method guarantees that only products meeting quality standards reach consumers.
Attribute | Description |
---|---|
100% Inspection Method Usage | To ensure every product is defect-free |
Purpose | To ensure every product is defect-free |
Ideal For | High-value products with low tolerance for defects |
Benefit | 100% assurance of product quality |
Quality Control Tools and Techniques
- Control Charts: One of the most widely used tools in QC, control charts track the variation in product measurements over time, identifying trends and shifts in production that may indicate underlying issues. These charts help distinguish between normal variation and special cause variation.
- Pareto Analysis: Based on the 80/20 rule, Pareto analysis helps identify the most common defects or issues that contribute to the majority of quality problems. By focusing on the most frequent issues, businesses can significantly improve overall product quality.
- Fishbone Diagram (Ishikawa): This tool helps identify the root causes of a quality issue. By categorizing potential causes into areas like people, processes, materials, and equipment, businesses can address the underlying problem rather than just the symptoms.
- Six Sigma: A method focused on reducing defects to a level where they are practically nonexistent (less than 3.4 defects per million opportunities). Six Sigma employs a disciplined, data-driven approach to eliminate errors and improve processes.
- Failure Mode and Effects Analysis (FMEA): FMEA is used to identify potential failure points in the design and manufacturing process and assess the impact of those failures on product quality. It helps prioritize areas for improvement based on their severity and likelihood of occurrence.
Advancements in technology, such as the Internet of Things (IoT), have Also revolutionized quality management systems. According to a Statista study,
“IoT-driven quality management in the UK alone brought significant benefits, with the manufacturing sector realizing savings of approximately 7.43 billion British pounds between 2015 and 2020. This illustrates how technology can enhance quality control processes, reduce costs, and improve overall efficiency."
Case Studies of QC Success Stories
Toyota
Toyota’s success can be largely attributed to its Toyota Production System (TPS), which emphasizes continuous improvement and high-quality standards. By implementing strict QC measures, Toyota has maintained its position as one of the most trusted car manufacturers worldwide.
The following study highlights how Toyota's focus on quality has not only enhanced customer satisfaction but also fostered a culture of continuous improvement within the organization.
Toyota's Approach to Quality Management: Tools and Techniques Published on September 11, 2023
Toyota’s success is rooted in the Toyota Production System (TPS), which emphasizes continuous improvement and high-quality standards. Core principles like Just-in-Time (JIT) and Jidoka streamline processes, reduce waste, and prevent defects. Toyota’s Kaizen philosophy empowers employees to suggest incremental improvements, while tools like Kanban ensure efficient inventory management. Collaborative supplier relationships and mistake-proofing techniques, such as Poka-Yoke, uphold consistent quality across the production chain. These practices have positioned Toyota as a global leader, renowned for reliability and innovation.
Samsung
Samsung's dedication to QC is evident in its production of smartphones and electronics. With rigorous testing procedures in place, including durability tests and battery safety checks, Samsung ensures that every product meets consumer expectations.
While the company has faced challenges, such as the Note 7 recall, it has learned from these experiences and implemented rigorous testing procedures to ensure product reliability and safety.
Key Quality Control Measures at Samsung:
- Durability Tests: Samsung subjects its products to a wide range of durability tests, including drop tests, bend tests, and extreme temperature tests, to ensure they can withstand real-world conditions.
- Battery Safety Checks: Battery safety is a critical aspect of Samsung's quality control. The company conducts extensive testing to prevent battery fires and explosions, as seen in the Note 7 incident.
- Software Updates: Samsung regularly releases software updates to address bugs, improve performance, and enhance security, demonstrating its commitment to product quality and customer satisfaction.
The Galaxy S Series: The Galaxy S series has consistently ranked among the top smartphones globally, thanks in part to Samsung's focus on quality and innovation. These devices undergo rigorous testing to ensure they meet high standards of performance and reliability.
The Galaxy Watch Series: Samsung's Galaxy Watch series has gained popularity for its durability and water resistance. The watches are tested in various conditions to ensure they can withstand the demands of daily wear and tear.
Pursuing a Career in Quality Control
Pathways & Salaries
QC careers offer opportunities for growth, especially for individuals who are detail-oriented and enjoy problem-solving. This field is essential for maintaining product quality and consistency across industries, offering a range of pathways and salary prospects.
Popular Certifications:
- Certified Quality Auditor (CQA): Certifies proficiency in auditing quality management systems.
- Certified Quality Engineer (CQE): Specializes in developing and applying quality engineering concepts.
- Six Sigma Certification: Focuses on process improvement and reducing defects through a data-driven approach.
Education & Experience:
- Entry-level QC positions typically require a high school diploma, but having a specialized degree or industry certification can set you apart.
- Experience is key to moving up in the field. After gaining foundational experience, individuals can progress to senior roles such as QC manager or director.
Salary Information:
Salaries in QC vary by industry and level of experience. According to the U.S. Bureau of Labor Statistics, the average salaries by industry as of May 2023 are as follows:
Industry | Average Salary |
---|---|
Manufacturing | $46,390 |
Wholesale Trade | $43,880 |
Professional Services | $48,680 |
Administrative Support | $35,940 |
Skills & Qualities Needed:
- Attention to Detail: A critical skill for identifying defects and ensuring product quality.
- Mechanical and Math Skills: Useful for understanding product specifications and assessing quality metrics.
- Physical Abilities: Ability to perform hands-on inspections.
- Technical Skills: Proficiency in operating QC equipment and analyzing data.
- Performance Under Pressure: QC professionals often work in high-stakes environments where quality standards must be upheld under tight deadlines.
Career Path:
- Entry-Level: Quality control associate or inspector.
- Mid-Level: QC specialist or senior associate, possibly with a focus on a specific product or process.
- Senior Roles: With additional experience, you may advance to positions such as QC manager or director, overseeing larger teams and implementing quality assurance strategies.
Leadership Positions:
- QA Systems Manager
- QA Operations Manager
- QA Compliance Manager
These positions can lead to executive roles such as:
- Director of Quality
- Head of Compliance
- Vice President of Quality
With experience, certifications, and continuous professional development, a career in QC can be financially rewarding and provide opportunities for leadership roles across industries.
Elevate Your QC Standards with Amrep Mexico!
Quality control is the cornerstone of any successful business, ensuring that products not only meet customer expectations but also comply with industry standards. By leveraging advanced methods and technologies, companies can streamline their QC processes, reduce costs, and build lasting customer trust.
Whether you’re considering a career in quality control or seeking to implement robust QC strategies in your business, understanding its principles and practices is essential.
AtAmrep Mexico Supplier Quality Services , we specialize in delivering Quality Management services that help businesses maintain product excellence. Our expertise ensures that your products meet the highest standards, providing consistency, reliability, and customer satisfaction.
Connect with us today to learn how we can enhance your QC processes and drive long-term success.